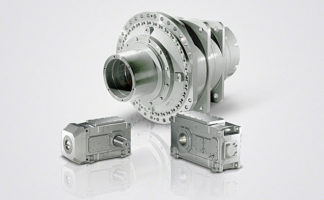
SINAMICS G180
Configuring instructions
Functions
5/2
Siemens D 18.1 · 2014
5
■
Overview
Communication with higher-level control and
customer terminal strip
A terminal strip compliant with NAMUR recommendation NE37
is provided as standard for the customer interface. Ethernet
(PROFIBUS with Ethernet-to-PROFIBUS converter board), PRO-
FIBUS DP, Modbus RTU, Modbus TCP and
CANopen interfaces are also available. A PROFINET-based
communication option is currently in development.
The NAMUR-compliant customer terminal strip can be used to
connect the converter to the higher-level controller using analog
and digital signals, or to connect additional units.
To simplify configuring and commissioning of the drive, various
applications can be selected and modified in the frequency
converter. The unit can also be parameterized individually at the
factory prior to delivery.
Further information and guidance are available in the IMS.
Open-loop and closed-loop control functions
The SINAMICS G180 converter can be operated in different
control modes:
•
Closed-loop control of the speed or torque of a drive by
appropriate machine commutation. In "space-vector control"
mode (SVC), the converter utilizes an optimized voltage/
frequency ratio. To meet the requirements of dynamic applica-
tions, machine commutation can be combined with a tacho-
generator to implement "field-oriented control" (FOC).
•
Closed-loop control of current or voltage at the converter out-
put. This mode of control does not involve machine commuta-
tion. The output frequency and the current or the voltage are
specified as setpoints and implemented in the converter
(within the tolerances of the unit).
Thanks to the integrated process controller, it is possible to
control a wide range of process variables in different control
modes.
Software and protective functions
The software functions available as standard are described below:
Software and protective functions
Description
Setpoint inputs
Setpoints can be input both internally and externally, i.e. internally as a fixed setpoint
or motorized potentiometer setpoint and externally via the communications interface or
an analog input on the customer terminal strip. The internal fixed setpoint and the
motorized potentiometer setpoint can be switched over or adjusted using control
commands via all interfaces.
Autotuning function
Thanks to the autotuning function (automatic measurement of the motor stator
resistance), the closed-loop drive control can be commissioned and optimized faster
and more easily.
Random pattern
Pulse pattern generation with or without random pattern can be selected. The purpose of
this function is to prevent dominant clock frequency noise in the motor.
Ramp-function generator
A convenient ramp-function generator with separately adjustable and switchable
ramping times, together with adjustable and switchable rounding times in the lower
and upper speed ranges (transition roundings 1 to 4), allows the drive to be smoothly
accelerated and braked. As a consequence, this avoids the drive train from being
overloaded and reduces the stress on mechanical components. The down ramps can
be parameterized separately for quick stop. In addition, all parameters can be switched
over for special operating ranges.
Overvoltage controller
The overvoltage limiting controller automatically prevents overvoltages in the DC link if
the down ramp is too short, for example. This may also extend the set ramp-down time.
Mains supply backup
In the event of supply voltage dips, the kinetic energy of the rotating drive is used to
buffer the DC link so as to prevent fault trips. The converter remains operational as long
as the drive can provide regenerative energy as a result of its motion and the DC link
voltage does not drop below the trip threshold. When the line supply recovers within a
parameterizable time, the drive is again accelerated up to its setpoint speed.
Undervoltage behavior
The operational performance of the frequency converter under line undervoltage
conditions can be influenced to a large extent.
The automatic restart function switches the drive on again when the power is restored
after a power failure, and ramps up to the current speed setpoint. The automatic restart
function is successful only if the power failure does not last longer than the para-
meterized T restart time.
Synchronization
It is possible to synchronize the SINAMICS G180 converter with a motor that is still
turning and to accelerate the motor to the specified setpoint.
Slip compensation
An automatic slip compensation function improves the speed accuracy of drives that are
not equipped with a speed encoder.
Process control
The integrated process controller can be used to implement simple control functions,
e.g. level control or volumetric flow control.
It is designed as a PID controller with separately settable P, I and D components.
Logic elements
The "Logic elements" function can be used to generate modal signals and to combine
signals using logic.
Message generators
Messages can be generated subject to predefined conditions.
Parameter switches
A parameter switch can be used to switch a parameter from its original value to an
alternative value.
Automatic acknowledgement function
Fault messages can be acknowledged fully automatically if required.
© Siemens AG 2014