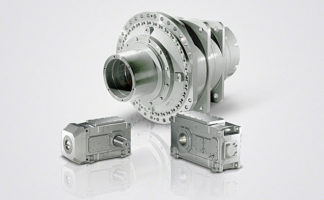
SINAMICS G180
Option descriptions
Standard options
4/19
Siemens D 18.1 · 2014
4
■
Options
(continued)
Y98
Controlled outgoing feeder for auxiliary drive up to max.
4 kW, please specify type of drive, voltage and number of
phases
With option
Y98
an outgoing feeder is prepared for an auxiliary
drive of up to 4 kW. Please specify the voltage and number of
phases as well as the type of drive or function description.
The outgoing feeder can be controlled internally by the
converter or externally.
Note:
The voltage for the auxiliary drive must be less than or equal to
the line voltage.
L72
Braking chopper
L72
Braking chopper integrated into converter
(braking resistor is not included and must be ordered separately)
During motor operation the electrical power flow is from the con-
verter to the motor. During generator operation the electrical
power flow is from the motor to the converter (braking of rotating
masses, active loads).
The standard version of SINAMICS G180 cannot feed energy
back into the system. During braking operation kinetic energy
can be converted into heat loss. Approx. 10 % of the braking
torque is available in the upper speed range. A braking torque
up to 50 % can be achieved without a supplementary device in
the mid and lower speed range through oversaturation of the
motor. The braking chopper accessory allows an external brak-
ing resistor to be connected. The braking torque varies in accor-
dance with the converter type and resistance value. The energy
generated is converted to heat via the braking transistor in the
braking resistor. Any questions regarding braking resistors and
the maximum possible braking torque should be addressed to
your Siemens contact person.
A thermal model of the braking resistor incorporated into the
converter firmware protects the resistor from overload.
L80, L81, L82, L83 and Y80
CALOMAT CK145
L80
CALOMAT CK145
The CALOMAT CK145 for monitoring motors, transformers, etc.
with PTC thermistor temperature sensors to DIN 44081, espe-
cially explosion-proof motors, is certified to ATEX 95 (Directive
94/9 EC). The requirements of EN 61800-5-1 – Basic require-
ments for protective separation in electrical equipment – are also
fulfilled in the sensor circuit and between the changeover con-
tacts. Destruction of the supervisory control system due to an
insulation fault on the PTC thermistor is almost totally prevented.
The CALOMAT in IP20 degree of protection is uniformly
22.5 mm wide and suitable for mounting on a standard rail to
DIN EN 50022. The two changeover contacts can be used for
disconnecting the system and for outputting alarms to a higher-
level control system. The status of the monitoring circuit is
signaled by LEDs for Operation (green) and Fault (red). The
CK145 also features a LED for sensor break or sensor short-
circuit.
The following generally applies:
•
CALOMAT thermal motor protection with ATEX certification.
•
Directive 94/9/EC, installed in the control cabinet.
•
Devices with protective separation to EN 61800-5-1.
•
The general health and safety requirements are fulfilled
due to compliance with
EN 60947-1/EN 60947-5-1/DIN VDE 0660 Part 302 and
Part 303/EN 60079-14.
•
Sensor circuit: max. 6 PTC thermistors (< 1.5 k
Ω
).
•
Acknowledgment button on device and remote acknowledge-
ment is possible.
Note:
When CALOMAT devices with a switch-off function are used, a
line contactor must be installed on the input side (option
S01
or
S02
) for compliance with ATEX 95 (Directive 94/9 EC).
CALOMAT devices are used in special cases, e.g. identical
design to previously supplied equipment, or for evaluating
several PTC thermistors. Otherwise, for evaluating PTC
thermistors, peripheral board 2 (option
G03
) or peripheral
board 4 (option
G05
) must be used.
© Siemens AG 2014