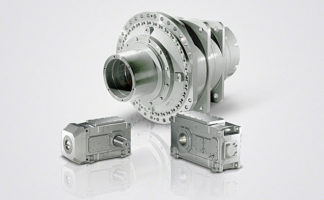
SINAMICS G150 NEMA
Engineering information
4
Siemens D11.7
(Part 1) – 2013
4/13
Interface for speed feedback encoder
When is a speed feedback encoder recommended?
SINAMICS G150 is capable of accurately controlling torque
at and near zero speed without a speed feedback encoder.
It can do so during motoring operation, i.e. for applications
without an overhauling load that applies torque to the motor.
A speed feedback encoder is therefore required only rarely.
A speed feedback encoder should be considered if one
or more of the following applies to the (usually constant
torque) application:
• Maximum speed accuracy
• Very high dynamic performance requirements
• Accurate control of torque below 5% speed (especially
with overhauling loads)
• High starting torque or high overloads at low speeds
(especially with overhauling loads)
The SMC30 sensor module is used to connect a digital speed
feedback encoder (for closed loop vector control).
[An SMC30 is not required when using a DRIVE-CLiQ encoder
or a motor with a DRIVE-CliQ interface and integral encoder].
TTL/ HTL incremental encoders with and without cable-break
detection are supported.
The motor temperature can also be detected using KTY84-
130 or PTC sensors.
The SMC30 sensor module has an encoder connection
including motor temperature detection (KTY84-130) via
SUB-D connector or terminals.
The maximum encoder cable length between SMC30
modules and encoders is 330 ft. For HTL encoders, this
length can be increased to 990 ft. if signals A+/A- and B+/B-
are evaluated and the power supply cable has a minimum
size of #18 AWG (0.75 mm
2
).
Maximum control wire size is #14 AWG (2.5 mm
2
).
SMC30 Sensor Module (options K50 and K52)