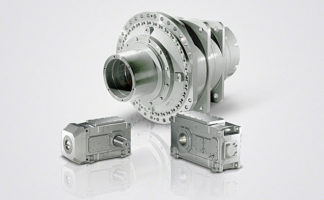
2/23
Siemens D 11 · 2015
2
Highlights
Communication
> PROFIdrive
■
Overview
PROFIdrive – the standardized drive interface for
PROFINET and PROFIBUS
PROFIdrive defines the device behavior and technique to
access internal device data for electric drives connected to
PROFINET and PROFIBUS – from basic frequency inverters
up to high-performance servo controllers.
It describes in detail the practical use of communication func-
tions – slave-to-slave data transfer, equidistance and clock cycle
synchronization (isochronous mode) in drive applications.
In addition, it specifies all device characteristics which influence
interfaces connected to a controller over PROFINET or
PROFIBUS. This also includes the state machine (sequence
control), the encoder interface, scaling of values, definition of
standard telegrams, access to drive parameters etc.
The PROFIdrive profile supports both central as well as distrib-
uted motion control concepts.
What are profiles?
For devices and systems used in automation technology, profiles
define properties and modes of behavior. This allows manufac-
turers and users to define common standards. Devices and sys-
tems that comply with such a cross-manufacturer profile, are in-
teroperable on a fieldbus and, to a certain degree, can be
interchanged.
Are there different types of profiles?
A distinction is made between what are known as application
profiles (general or specific) and system profiles:
•
Application profiles (also device profiles) predominantly refer
to devices (e.g. drives) and include and agreed selection
regarding bus communication as well as also specific device
applications.
•
System profiles describe classes of systems, including master
functionality, program interfaces and integration resources.
Is PROFIdrive fit for the future?
PROFIdrive has been specified by the PROFIBUS and
PROFINET International (PI) user organization, and is specified
as a standard that is fit for the future through standard
IEC 61800-7.
The basic philosophy: Keep it simple
The PROFIdrive profile tries to keep the drive interface as simple
as possible and free from technology functions. As a result of
this philosophy, referencing models as well as the functionality
and performance of the PROFINET/PROFIBUS master have ei-
ther no influence or only a low influence on the drive interface.
One drive profile – different application classes
The integration of drives into automation solutions depends very
strongly on the particular drive application. In order to be able to
address the complete, huge bandwidth of drive applications –
from basic frequency inverters up to synchronized multi-axis
systems with a high dynamic performance – using just one pro-
file, PROFIdrive defines six application classes, to which most
drive applications can be assigned:
•
Class 1 – standard drives (for example pumps, fans, agitators
etc..)
•
Class 2 – standard drives with technological functions
•
Class 3 – positioning drives
•
Class 4 – motion control drives with central, higher-level
motion control intelligence and patented position control
concept "dynamic servo control"
•
Class 5 – motion control drives with central, higher-level
motion control intelligence and position setpoint interface
•
Class 6 – motion control drives with distributed motion control
intelligence integrated in the drives themselves
■
Design
The device model of PROFIdrive
PROFIdrive defines a device model based on function modules
which cooperate in the device and generate the intelligence of
the drive system. These modules have objects assigned to them
which are described in the profile and are defined with respect
to their functions. The overall functionality of a drive is therefore
described through the sum of its parameters.
In contrast to other drive profiles, PROFIdrive defines only the
access mechanisms to the parameters as well as a subset of
profile parameters (approx. 30) such as the fault buffer, drive
control and device identification.
All other parameters are vendor-specific which gives drive man-
ufacturers great flexibility with respect to implementing function
modules. The elements of a parameter are accessed acyclically
via data records.
As a communication protocol, PROFIdrive uses DP-V0, DP-V1,
and the DP-V2 expansions for PROFIBUS including the functions
"Slave-to-Slave Communication" and "Isochronous Operation",
or PROFINET IO with real-time classes RT and IRT.
■
More information
Further information on PROFINET and PROFIBUS is available at
www.profibus.com
See under Download / Technical description & books /
PROFIdrive – Technology and Application - System Description
G_PM10_EN_00133
Clock synchronism
Status Word + Actual Position ...
Control Word + Speed Setpoint + ...
Encoder
Encoder
Encoder
M
M
M
Closed Loop Speed Ctrl.
Drive
Closed Loop Speed Ctrl.
Drive
Closed Loop Speed Ctrl.
Drive
Clock
Application Class 4
Interpolation
Pos. Control
Technology
Automation
© Siemens AG 2015