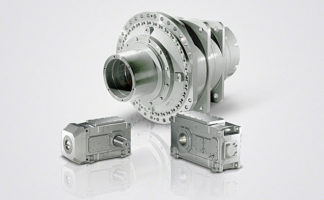
2/5
Siemens D 11 · 2015
■
Function
(continued)
2
Highlights
Safety Integrated
Safe Operating Stop (SOS)
With the SOS function, the stopped motor is held in position and
monitored by drive control.
Activation
The SOS function constitutes safe standstill monitoring. The
drive control remains in operation. The motor can therefore de-
liver the full torque to hold the current position. The actual posi-
tion is reliably monitored. In contrast to safety functions SS1 and
SS2, the speed setpoint is not influenced autonomously. After
SOS has been activated, the higher-level control must bring the
drive to a standstill within a parameterized time and then hold
the position setpoint.
Application
SOS is an ideal solution for all those applications for which the
machine or parts of the machine must be at a safe standstill for
certain steps, but the drive must also supply a holding torque. It
is ensured that despite counter torque the drive remains in its
current position. In contrast to SS1 and SS2, the drive does not
brake autonomously in this case. It expects the higher-level con-
troller to ramp down the relevant axes as a coordinated group
within an adjustable delay time. This can be used to prevent any
damage to the machine or product. Typical applications for SOS
include winders, converting and packaging machines and ma-
chine tools.
Customer benefits
No mechanical components are necessary to keep the axis in
position despite any counterforce that may occur. Due to the
short switching times and the fact that the drive control always
remains active, setup and downtimes are reduced. Recalibra-
tion of the axis after exiting the SOS function is not necessary.
The axis can immediately be moved again after deactivation of
the SOS function.
Safe Brake Control (SBC)
The SBC function permits the safe control of a holding brake.
SBC is always activated in parallel with STO.
Activation
A holding brake which is active in a de-energized state is con-
trolled and monitored using safe two-channel technology. Due to
the two-channel control, the brake may still be activated in the
event of an insulation fault in the control cable. Errors of this kind
are detected early by means of test pulses.
Notes
An additional Safe Brake Relay is required for power units in
blocksize format. An additional Safe Brake Adapter is necessary
for power units in chassis format.
Application
The SBC function is used in conjunction with the functions STO
or SS1 to prevent the movement of an axis in the torque-free
state, e.g. because of gravity.
Customer benefits
Again, the function saves the use of external hardware and the
associated wiring.
G_D211_XX_00207
s
t
SOS
∆t
v
t
G_D211_XX_00276
STO
SBC
© Siemens AG 2015