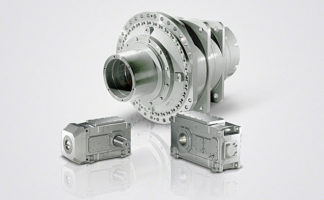
5/6
Siemens D 11 · 2015
5
Tools and configuration
STARTER commissioning tool
■
Overview
The user-friendly STARTER commissioning tool can be used for:
• Commissioning
• Optimization
• Diagnostics
This software can be operated as a standalone PC application,
or integrated as a TIA-compatible program in SIMATIC STEP 7,
or highly integrated into the SCOUT Engineering System
(for SIMOTION). The basic functions and handling are the same
in both cases.
In addition to the SINAMICS drives, STARTER also supports
MICROMASTER 4 devices.
The project wizards can be used to create the drives within the
structure of the project tree.
Beginners are supported by solution-based dialog guidance,
whereby a standard graphics-based display maximizes clarity
when setting the drive parameters.
First commissioning is guided by a wizard which makes all the
basic settings in the drive. Therefore, getting a motor up and run-
ning is merely a question of setting a few of the drive parameters
as part of the drive configuration process.
The individual settings required are made using graphics-based
parameterization screens, which also precisely visualize the
principle of operation of the drive.
Examples of individual settings that can be made include:
•
How terminals are used
•
Bus interface
•
Setpoint channel (e.g., fixed setpoints)
•
Closed-loop speed control (e.g., ramp-function generator,
limits)
•
BICO interconnections
• Diagnostics
For experts, the expert list can be used to specifically and
quickly access individual parameters at any time. An individual
compilation of frequently used parameters can be saved in ded-
icated user lists and watch tables.
In addition, the following functions are available for optimization
purposes:
•
Self-optimization of the controller settings
(depending on drive unit)
•
Setup and evaluation of trace recordings
1)
Tool function for recording 2 × 8 signals with
- Measuring cursor function
- Extensive trigger functions
- Several Y scales
- Sampling times in the current controller cycle clock
Diagnostics functions provide information about:
•
Control/status words
•
Parameter status
•
Operating conditions
•
Communication states
Performance features
•
User-friendly: Only a small number of settings need to be
made for successful first commissioning: The motor starts to
rotate
•
Solution-oriented dialog-based user guidance simplifies
commissioning
•
Self-optimization functions reduce manual effort for optimi-
zation.
Minimum system requirements
The following minimum requirements must be complied with:
• Hardware
- PG or PC with Pentium III min. 1 GHz
(recommended >1 GHz)
- Work memory 1 GB (2 GB recommended)
- Screen resolution 1024 × 768 pixels, 16-bit color depth
- Free hard disk memory: min. 3 GB
• Software
- Microsoft Internet Explorer V6.0 or higher
- 32-bit operating systems:
Microsoft Windows XP Professional SP3
Microsoft Windows 7 Professional incl. SP1
Microsoft Windows 7 Ultimate incl. SP1
Microsoft Windows 7 Enterprise incl. SP1
(standard installation)
- 64-bit operating systems:
Microsoft Windows 7 Professional SP1
Microsoft Windows 7 Ultimate SP1
Microsoft Windows 7 Enterprise SP1 (standard installation)
Microsoft Windows Server 2008 R2 SP1
■
Integration
Data can be exchanged (depending on the version) via
PROFIBUS or PROFINET/Ethernet or via a serial interface.
For commissioning and service, a PG/PC can be connected to
the CU320-2 Control Unit via PROFIBUS. A PROFIBUS connec-
tion must be available with a connecting cable at the PG/PC.
Further, communication between a CU320-2 Control Unit and
PG/PC can also be established via Ethernet, either via an
(optional) CBE20 Communication Board or the Ethernet
interface -X127 on the CU320-2 Control Unit.
Note:
The terminal strip -X127 is suitable as a communication link to
the PG/PC only for the purposes of servicing and commission-
ing.
1)
Depending on drive unit.
Not supported for MICROMASTER 4, SINAMICS G110,
SINAMICS G120 <firmware V4.4, SINAMICS G110D and
SINAMICS G120D <firmware V4.5.
© Siemens AG 2015