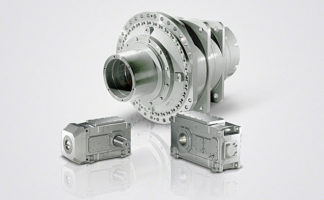
3/7
Siemens D 35 · 2017
■
Design
(continued)
3
System configuration
SINAMICS G120P and SINAMICS G120P Cabinet pump, fan, compressor converters
SINAMICS G120P and SINAMICS G120P Cabinet pump, fan, compressor converters
DC link components
The following DC link components are available for the
SINAMICS G120P converters:
•
Braking Module for PM330 Power Modules and
SINAMICS G120P Cabinet
A Braking Module and the matching braking resistor are
required to achieve controlled braking of a drive. The Braking
Module houses the power electronics and the associated
control circuit.
•
Braking resistors for PM330 Power Modules and
SINAMICS G120P Cabinet
Excess energy in the DC link is dissipated via the braking
resistor.
Load-side power components
Various load-side power components are available for the
SINAMICS G120P converters. These allow the use of longer
shielded motor cables and increase the motor service life:
•
Output reactors
Output reactors reduce the rate of voltage rise (
dv/dt
) and the
height of the current peaks, and enable longer motor cables
to be connected.
•
Sine-wave filters for PM230 Power Modules
Sine-wave filters limit the rate of voltage rise (
dv/dt
) and the
peak voltages on the motor winding. Similar to an output
reactor, they enable the connection of longer motor cables.
•
dv/dt filters plus VPL for PM240P-2 and PM330 Power
Modules
dv/dt filters plus VPL (Voltage Peak Limiter) limit the voltage
rate-of-rise dv/dt to values <500 V/
μ
s and the typical voltage
peaks to values according to the limit value curve as per
IEC/TS 60034-17: 2006.
Standard motors with standard insulation and without
insulated bearings can be used for converter operation if a
dv/dt filter plus VPL is used.
•
dv/dt filters compact plus VPL for PM330 Power Modules and
SINAMICS G120P Cabinet
dv/dt filters compact plus VPL (Voltage Peak Limiter) limit the
voltage rate-of-rise dv/dt to values of <1600 V/
μ
s and the
typical voltage peaks to values according to the limit value
curve A to IEC 60034-25: 2007.
Standard motors with standard insulation and without
insulated bearings can be used for converter operation if a
dv/dt filter compact plus VPL is used.
Optional accessories
•
Line-side cable connection, left, for PM330 Power Modules
•
Push Through mounting frame for PM230 Power Modules
•
SINAMICS memory card (SD card)
•
PC inverter connection kit 2
•
Shield connection kits for CU230P-2 Control Units
(for PM230 and PM240P-2 Power Modules)
•
Shield connection kits and shield plates for PM230 and
PM240P-2 Power Modules
Spare parts
•
Spare part kit for Control Units
•
Shield connection kits for PM240P-2 Power Modules
•
Shield plates for PM230 Power Modules
•
Mounting set for PM230 Power Modules
•
Terminal Cover Kit for PM230 Power Modules
•
Fan units and replacement fans
■
Function
Technology function
Functions specific to pumps, fans and compressors are already
integrated, e.g.:
•
Automatic restart
Application restart after a power failure or fault occurrence
•
Flying restart
Connection of the converter when the motor is running
•
Flux reduction
Automatic adaptation of the motor current to the prevailing
load conditions in U/f control mode (ECO mode) as well as in
sensorless vector control mode
•
Cascade connection
Load-dependent connection and disconnection of a
maximum of three additional motors by the converter in order
to provide a largely constant output power (implemented by
means of an additional external circuit)
•
Hibernation mode
Startup or shutdown of the drive when the relevant value drops
below an external setpoint or the internal PID controller
setpoint
•
Real-time clock
For time-dependent process controls, e.g. to reduce the
temperature of a heating control at night and with automatic
daylight saving/standard time switchover
•
Freely programmable logical function blocks
For simulating simple PLC functions
Functions especially for building technology as well as heating/
air conditioning/ventilation applications
•
4 integrated PID controllers
One PID controller for controlling the drive speed as a function
of pressure, temperature, flowrate, fill level, air quality and
other process variables, and a further three PID controllers
with freely configurable outputs, e.g. for controlling valves
(heating, cooling) or flaps
•
Emergency mode
Special converter operating mode that enhances the avail-
ability of the drive system in the event of a fire
•
Multi-zone controller
- Closed-loop control of a zone with up to 3 sensors for
pressure or temperature, or
- Closed-loop control of two independent zones, each with
one sensor
•
Bypass mode
When the setpoint is reached or a fault occurs, the system
changes over to line operation (implemented by means of an
additional external circuit)
•
Programmable time switches
© Siemens AG 2017