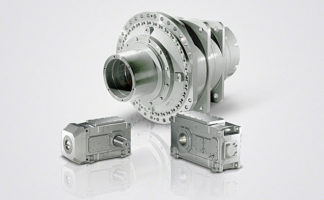
5/14
Siemens D 35 · 2017
■
Options
(continued)
5
SINAMICS G120P Cabinet, converter cabinet units
SINAMICS G120P Cabinet, 75 kW to 630 kW
SINAMICS G120P Cabinet
F03, F71, F75, F77, F97
Equipment acceptance in the presence of the customer
F72, F74, F76
Equipment acceptance without the presence of the
customer
K69
Switchover to a 120 V AC auxiliary power supply
With this option, the supply voltage range is adjusted to all rele-
vant loads in the control cabinet to 110 V AC to 120 V AC, e.g.
for fans and monitoring devices.
If the supply voltage is made available in the cabinet via the op-
tion
K74
, the voltage range is also adjusted to 110 V to 120 V.
K74
Provision of a cabinet-internal 230 V AC auxiliary power
supply
If there is no 230 V AC power supply in the customer installation,
option
K74
can be used to provide a cabinet-internal auxiliary
power supply for the required auxiliary voltages of the external
control circuits of the cabinet unit. The auxiliary voltages are
generated by a transformer.
Note:
If there is no 230 V AC power supply in the customer installation,
it is essential to select option
K74
in order to ensure proper func-
tioning of the options
L01, L13, L19, L57, L60, L83, L84
and
L86
and for the options
M23, M43
and
M54
for cabinet version A and
for option
M21
for cabinet version A, frame sizes F and HX!
Options
L50
and
L55
always require an external supply voltage
and must not be supplied via option
K74
.
K83
Stop Category 0 (STO)
This option enables the Safe Torque Off (STO) safety function for
the drive.
The implemented safety technology allows for short-circuit and
cross-circuit detection. Connection contacts are provided for
the user on a terminal block for connecting two channel safety
sensors. A start or acknowledgement button can also be
connected via terminal block.
K84
Stop Category 1 (SS1)
This option enables time-controlled braking of the motor (SS1)
according to a braking ramp (0,5 - 30 s) with subsequent Safe
Torque Off (STO).
The implemented safety technology allows for short-circuit and
cross-circuit detection. Connection contacts are provided for
the user on a terminal block for connecting two channel safety
sensors. A start or acknowledgement button can also be
connected via terminal block.
K96
CU230P-2 Control Unit PROFINET, EtherNet/IP
The converter is shipped with a CU230P-2 PN Control Unit
(PROFINET).
For more information about the CU230P-2 PN Control Unit,
refer to SINAMICS G120P built-in and wall-mounted units.
K97
CU230P-2 Control Unit PROFIBUS
The converter is shipped with a CU230P-2 DP Control Unit
(PROFIBUS).
For more information about the CU230P-2 DP Control Unit,
refer to SINAMICS G120P built-in and wall-mounted units.
K98
CU230P-2 HVAC Control Unit
The converter is shipped with a CU230P-2 HVAC Control Unit
(USS, Modbus RTU, BACnet MS/TP, FLN P1).
For more information about the CU230P-2 HVAC Control Unit,
refer to SINAMICS G120P built-in and wall-mounted units.
Option
Description
F03
Visual acceptance
The tests are carried out with the converter de-energized.
The following is included in the scope of the acceptance
tests:
• Checking the degree of protection
• Checking the equipment (components)
• Checking the equipment identifiers
• Checking clearance and creepage distances
• Checking cables
• Checking customer documentation
• Submission of the acceptance report
F71, F72
Function test with no
motor connected
After the visual inspection with the converter switched off,
the converter is connected to rated voltage. No current at
the converter output end.
The following is included in the scope of the acceptance
tests:
• Visual inspection as described for option
F03
• Checking power supply
• Checking protective and monitoring devices (simulation)
• Checking fans
• Precharging test
• Function test without connected motor
• Submission of the acceptance report
F74, F75
Function test with
test bay motor under no-load
conditions
After the visual inspection with the converter switched off,
the converter is connected to rated voltage. A small cur-
rent flows at the converter's output in order to operate the
test bay motor under no-load conditions.
The following is included in the scope of the acceptance
tests:
• Visual inspection as described for option
F03
• Checking power supply
• Checking protective and monitoring devices (simulation)
• Checking fans
• Function test with test bay motor under no-load
conditions
• Submission of the acceptance report
F76, F77
Acceptance of insulation test of the converter
The following is included in the scope of the acceptance
tests:
• High-voltage test
• Measurement of the insulation resistance
• Submission of the acceptance report
F97
Customer-specific system acceptance tests
(on request)
If acceptance tests are desired which are not covered by
the options
F03
,
F71/F72
,
F74/F75
or
F76/F77
, customer-
specific acceptance tests/supplementary tests can be
ordered using order code
F97
on request and following
technical clarification.
© Siemens AG 2017