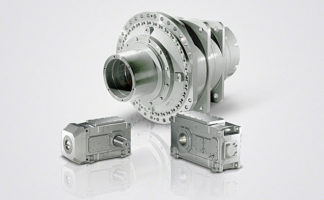
SINAMICS DCM
Accessories and supplementary components
SMC30 Sensor Module Cabinet-Mounted
4/4
Siemens D 23.1 · 2014
4
■
Overview
Every CUD (both Standard CUD as well as also Advanced CUD)
can evaluate the signals of an incremental encoder. For applica-
tions where more than one encoder must be evaluated, either a
second CUD and/or SMC30 Sensor Module Cabinet-Mounted
can be used.
The SMC30 can be used to evaluate SSI encoders with incre-
mental signals, which for instance, are used for positioning
functions.
Encoders, which have a DRIVE-CLiQ interface, cannot be
evaluated at the SINAMICS DC MASTER or at the SMC30.
These encoders are usually not used in DC drive technology.
The following encoder signals can be evaluated:
•
Incremental encoders TTL/HTL with and without broken cable
detection (broken cable detection is only available with
bipolar signals)
•
SSI encoder with TTL/HTL incremental signals
•
SSI encoder without incremental signals
The motor temperature input, available on the SMC30, is not
evaluated for SINAMICS DC MASTER. A motor temperature
sensor can be evaluated using the temperature measurement
input provided on each CUD.
■
Design
The SMC30 Sensor Module Cabinet-Mounted features the
following interfaces as standard:
•
1 DRIVE-CLiQ interface
•
1 encoder connection via Sub-D connector or terminals
•
1 connection for the electronics power supply via the 24 V DC
power supply connector
•
1 PE/protective conductor connection
The status of the SMC30 Sensor Module Cabinet-Mounted is
indicated via a multi-color LED.
The SMC30 Sensor Module Cabinet-Mounted can be snapped
onto a TH mounting rail in accordance with EN 60715
(IEC 60715).
The maximum encoder cable length between SMC30 modules
and encoders is 100 m. For HTL encoders, this length can be in-
creased to 300 m if the A+/A- and B+/B- signals are evaluated
and the power supply cable has a minimum cross-section of
0.5 mm
2
.
The signal cable shield can be connected to the SMC30 Sensor
Module Cabinet-Mounted via a shield connection terminal, e.g.
Phoenix Contact type SK8 or Weidmüller type KLBÜ CO 1.
■
Integration
The SMC30 Sensor Module Cabinet-Mounted communicates
with the Advanced CUD via DRIVE-CLiQ.
One SMC30 can be connected to each Advanced CUD.
■
Technical specifications
■
Selection and ordering data
Note:
The maximum permissible encoder currents should be carefully
observed. The capacitive recharging currents increase in the
connecting cable between the encoder and converter due to
long cable lengths and high output frequencies. This can cause
the output driver of the encoder to be overloaded and/or result
in incorrect evaluation of the encoder signals. This is the reason
that the encoder manufacturer's instructions must be carefully
observed.
SMC30 Sensor Module Cabinet-Mounted
Current consumption, max.
at 24 V DC, not taking into account
the encoder
0.2 A
• Conductor cross-section, max.
2.5 mm
2
• Fuse protection, max.
20 A
Power loss
< 10 W
Encoders that can be evaluated
• Incremental encoder TTL/HTL
• SSI encoder with TTL/HTL
incremental signals
• SSI encoder without incremen-
tal signals
• Encoder supply
24 V DC/0.35 A or
5 V DC/0.35 A
• Encoder frequency, max.
300 kHz
• SSI baud rate
100 … 250 kBaud
• Limiting frequency
300 kHz
• Resolution absolute position SSI
30 bits
• Cable length, max.
-
TTL encoder
100 m (only bipolar signals
permitted)
1)
-
HTL encoder
100 m for unipolar signals
300 m for bipolar signals
1)
-
SSI encoder
100 m
PE connection
M4 screw
Dimensions
• Width
30 mm
• Height
150 mm
• Depth
111 mm
Weight, approx.
0.45 kg
Approvals
cULus (File No.: E164110)
Description
Article No.
SMC30 Sensor Module
Cabinet-Mounted
(without DRIVE-CLiQ cable)
6SL3055-0AA00-5CA2
1)
Signal cables twisted in pairs and shielded.
© Siemens AG 2014