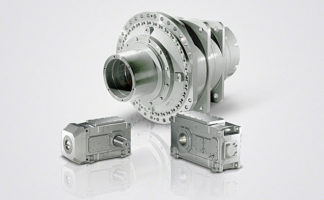
SINAMICS DCM
DC Converter and Control Module
DC Converter
3/51
Siemens D 23.1 · 2014
3
■
More information
(continued)
Safety shutdown (E-STOP)
The E-STOP function is used to open the relay contact for the
main contactor control within approximately 15 ms indepen-
dently of semiconductor components and the correct function-
ing of the CUD. If the CUD is operating correctly, entering
I
= 0
via the control ensures that the main contactor is switched in a
no-current condition. The drive coasts down once E-STOP has
been entered.
After the E-STOP has been reset, the drive goes into the "switch-
on inhibit" operating state. This must be acknowledged by
activating the "shutdown" function e.g. by opening terminal
switch-on/shutdown
.
Note:
The E-STOP function is not an EMERGENCY OFF function in the
sense of EN 60204-1.
Serial interfaces
The following serial interfaces are available for each CUD:
•
A serial interface on the Standard CUD and Advanced CUD
for the USS protocol according to RS232 or RS485 to connect
the optional AOP30 Advanced Operator Panel or for STARTER
via a PC.
•
A serial interface at the terminals of the Standard CUD and
Advanced CUD, RS485 two-wire or four-wire for a peer-to-
peer connection.
•
PROFIBUS DP as standard on the Standard CUD and
Advanced CUD
•
PROFINET via the CBE20 Communication Board on the
Advanced CUD (option)
•
EtherNet/IP via the CBE20 Communication Board on the
Advanced CUD (option)
•
DRIVE-CLiQ on Advanced CUD (option) to connect optional
SINAMICS components SMC30, TM15, TM31 and TM150
Physics of the interfaces
• RS232:
±
5 V interface for the point-to-point connection
•
RS485: 3.3 V common mode interface, interference-proof,
additionally for one bus connection with a maximum of
31 participants connected to the bus
USS protocol
Open Siemens protocol, can be simply programmed e.g. on the
PC in third-party systems, any master interfaces can be used.
The drives operate as slaves connected to a master. The drives
are selected using a slave number.
The following data exchange is possible via the USS protocol:
•
PKW data to read and write parameters
•
PZD data (process data) such as control words, setpoints,
status words, actual values
The send data (actual values) are selected by entering connec-
tor numbers in the parameters, the receive data (setpoints) re-
present the connector numbers, that can act at any intervention
points.
Peer-to-peer protocol
The peer-to-peer protocol is used to connect devices with one
another. For this operating mode, data is exchanged between
converters via a serial interface, e.g. to establish a setpoint
cascade. By using a serial interface as four-wire cable, data can
be received from the previous unit that is then processed (e.g.
by being multiplied) and then transferred to the following unit.
Only one serial interface is used for this purpose.
The following data can be exchanged between converters:
•
Sending control words and actual values.
•
Receiving status words and setpoints.
In this case, up to five data words are transferred in both the
send and receive directions. Data is exchanged via connector
numbers and intervention points.
The serial interfaces can be simultaneously operated. A connec-
tion to the automation (USS protocol) can be established via the
first interface for control, diagnostics and to enter the main set-
point. A second interface is used to realize a setpoint cascade
function via the peer-to-peer protocol.
Control terminal block
Terminals on the CUD
• Reference voltage P10, 10 mA load rating,
Reference voltage N10, 10 mA load rating
• 2 analog inputs via differential amplifier,
resolution
±
14 bits
0 ...
±
10 V, 0 ...
±
20 mA, 4 ... 20 mA
• 1 analog input via differential amplifier,
resolution
±
14 bits
0 ...
±
10 V
• 4 analog inputs via differential amplifier,
resolution
±
11 bits
0 ...
±
10 V
• One analog input for motor temperature sensor via PT100,
PTC or KTY84
• 2 analog outputs, referred to ground, 0 ...
±
10 V,
±
15-bit resolution,
max. 2 mA
• Pulse encoder evaluation for 5 or 24 V encoder, 2 tracks and zero
mark, maximum frequency 300 kHz
• P15 power supply, 200 mA for a pulse encoder
• 4 binary inputs, referred to ground, 2 with selectable function
• 4 binary inputs/outputs, referred to ground, outputs with open emitter
P24, 100 mA load rating
• 4 binary outputs, referred to ground, open emitter P24, 100 mA
load rating
• One serial interface, RS485 two-wire or four-wire, max. 187.5 kBaud
• P24 power supply to control the binary inputs
• Terminals for equipment ground "digital" (e.g.: to connect the loads
of the binary outputs)
• Terminals for equipment ground "analog " (e.g.: to connect the
reference potentials of analog inputs)
• Connector to connect an AOP30
• Connector to connect a serial RS232 interface and a 5 V power
supply, 300 mA (e.g.: for a pulse encoder)
Terminals on the gating module
• Analog tachometer 8 to 270 V for maximum speed
• E-STOP
© Siemens AG 2014