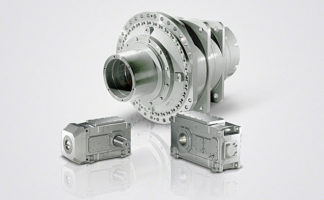
SINAMICS DCM
DC Converter and Control Module
DC Converter
3/49
Siemens D 23.1 · 2014
3
■
More information
(continued)
Optimization run
The SINAMICS DC MASTER converter units are supplied with
the factory settings. Controller setting is supported by selecting
automatic optimization runs. The selection is made using special
key numbers.
The following controller functions can be set using an automatic
optimization run:
•
Current controller optimization run to set the current controller
and pre-controls (armature and field circuit).
•
Speed controller optimization run for setting the speed con-
troller characteristics; automatic recording of the friction and
moment of inertia compensation for the speed controller
pre-control.
•
Automatic recording of the field characteristic for an EMF-
dependent field-weakening control and automatic optimiza-
tion of the EMF controller for field-weakening operation.
•
In addition, all of the parameters set during the automatic
optimization runs can be changed via the operator panel.
Monitoring and diagnostics
Displaying operating values
The operating state of the converter is displayed using a para-
meter. Several hundred signals can be displayed via parameter
or selected for output on the display unit. Examples of measured
values that can be displayed: Setpoints, actual values, status of
binary inputs/outputs, line supply voltage, line frequency, firing
angle, inputs/outputs of the analog terminals, controller input
and output, limits.
Trace function
Up to eight measured quantities can be saved by selecting the
trace function. A measured quantity or the occurrence of a fault
signal can be parameterized as trigger condition. By selecting a
trigger delay, it is also possible to record (trace) the pre-history
and post-history of events. The sampling time of the measured
value storage can be parameterized.
The measured values can be output via the serial interfaces
using the STARTER commissioning tool.
Fault messages
A number is assigned to each fault message. In addition, the
operating hour of the event is saved together with the fault mes-
sage. This allows the cause of the fault to be quickly pinpointed.
By using the optional AOP30 Advanced Operator Panel, fault
messages can be stamped in real time. Then, instead of the
operating hour of the event, the day and the time of day of the
event is displayed in the AOP30 fault list. For diagnostic pur-
poses, the last eight fault messages are saved with fault number,
fault value and the operating hours.
When a fault occurs
•
the binary output function "Fault" is set to LOW (user-assign-
able function),
•
the drive is switched off (controller inhibit, current
I
= 0 is
entered, pulses are inhibited, the relay "line contactor CLOSE"
drops out) and
•
an F is displayed with fault number, LED "Fault" is lit.
Fault messages should either be acknowledged via the operator
panel, a binary user-assignable terminal or a serial interface.
The "switch-on inhibit" state is reached after the fault has been
acknowledged. "Switch-on inhibit" is canceled by an OFF
command.
Automatic restart: An automatic restart is possible within a time
that can be parameterized between 0 and 10 s. If the time is set
to zero, a fault message is immediately output (for power failure)
without a restart. A restart can be selected for the following fault
messages: Phase failure (field or armature), undervoltage, over-
voltage, electronics power supply failure, undervoltage condi-
tion at the parallel SINAMICS DC MASTER.
A distinction is made between the following groups of fault
messages:
•
Power system faults: Phase failure, fault in the field circuit,
undervoltage, overvoltage, line frequency < 45 or > 65 Hz
•
Interface faults: CUD interfaces or interfaces to the supple-
mentary boards faulted
•
Drive faults:
Controller monitoring for speed controller,
Current controller, EMF controller,
Field current controller has responded,
Drive stalled,
No armature current possible
•
Electronic motor overload protection (
I
2
t
monitoring of the
motor has responded)
•
Tachometer monitoring and overspeed signal
•
Commissioning fault
•
Fault on the electronics module
•
Fault message from the thyristor check: This fault message
can only occur if the thyristor check has been activated using
the appropriate parameter. In this case, a check is made as to
whether the thyristors can be blocked and whether they can
be fired.
•
Fault messages from the motor sensor system:
Monitoring of brush length, bearing condition, air flow, motor
temperature
•
External faults via binary user-assignable terminals
The fault messages can be individually deactivated using a
parameter. Some fault messages are already deactivated in the
factory and can be activated using this parameter.
Alarms
Alarm messages display special states; however, they do not
cause the drive to be switched off. Alarms that occur do not have
to be acknowledged, but rather they are automatically reset as
soon as the cause of the alarm is no longer present.
When one or several alarms occur
•
the binary output function "Alarm" is set to LOW (user-assign-
able function) and
•
the alarm is displayed by the flashing "Fault" LED.
A distinction is made between the following groups of alarms:
•
Motor overtemperature: The calculated
I
2
t
value of the motor
has reached 100 %.
•
Alarms from the motor sensor system: Monitoring of brush
length, bearing condition, motor fan, motor temperature
•
Drive alarms: Drive has stalled, no armature current
possible
•
External alarms via binary user-assignable terminals
•
Alarms from supplementary modules
© Siemens AG 2014