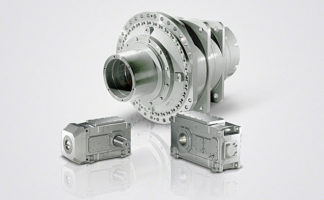
SINAMICS DCM
DC Converter and Control Module
DC Converter
3/34
Siemens D 23.1 · 2014
3
■
Options
(continued)
Ordering examples
Example 1
Application:
A DC drive system is required for a cableway. A SINAMICS
DC MASTER is to handle the closed-loop control of the selected
560 kW DC motor with a rated armature voltage of 420 V and a
rated armature current of 1306 A. Due to the overdimensioning
of 25 % specified by the acceptance authorities, and due to the
maximum ambient temperature of 45 °C that can occur, the
rated current of the converter had to be further reduced by 5 %.
This is the reason that a unit with a rated supply current of
2000
A was selected. The converter capable of energy recovery
is to be connected to a 400 V line supply. A PROFINET connec-
tion is required for the higher-level control.
Solution:
The four-quadrant converter with 2000 A and 400 V AC must be
selected for this application. The incremental encoder to sense
the speed – mounted on the motor – is directly evaluated in the
CUD of the SINAMICS DC MASTER, without requiring any
additional option.
The following options must be selected in order to permit the
PROFINET connection:
G00
(Advanced CUD left)
G20
(PROFINET Communication Board CBE20 left)
The ordering data are as follows:
6RA8095-4DV62-0AA0-Z
G00+G20
Example 2
Application:
An unwinder for paper in a reeler-slitter is to be modernized –
but the existing motor is to be kept. The power section is to be
supplied from the existing 690 V supply. The technological con-
trol is to be implemented in the higher-level PCS7 system. The
client specified PROFIBUS as the control and setpoint interface.
The following measured values and status displays are to be
visualized in the cabinet doors of the drive cabinet to facilitate
fast and simple diagnostics for the service and maintenance
personnel: Armature current, armature voltage, speed, field
current, status messages – operation and fault.
The customer explained that he repeatedly had problems with
the existing converter relating to overvoltage in the motor arma-
ture circuit – and as a consequence, this resulted in tension
fluctuations in the paper web when the motor went into the field-
weakening range. As a result of instability in the control voltage
supply, in the past, there were repeatedly failures that had a
negative impact on the availability.
Solution:
As a result of the data of the existing motor and the customer
specifications relating to acceleration and braking ramps, tam-
bour roll weight and maximum diameter, a four-quadrant con-
verter was selected with a rated supply voltage of 690 V and a
rated current of 1500 A. The dynamic overload capability of the
units is utilized to brake the drive when the paper web breaks.
The technological control with current setpoint interface is
realized in the higher-level control. This is the reason that for this
particular application, the Standard CUD is sufficient, which
already has an integrated PROFIBUS interface.
The problem with armature overvoltages when entering the field
weakening range has now been resolved by selecting the two-
quadrant field power section option. By actively reducing the
current using a counter-voltage, the field current actual value
can now follow the field current setpoint – even for steep accel-
eration ramps – and therefore overvoltages are avoided in the
armature circuit. The tension fluctuations in the paper web are
consequentially eliminated.
Selecting the option "electronics power supply for connection to
24 V DC" means that the drive system can be integrated into a
favorably-priced and low-maintenance DC UPS system com-
prising SITOP components.
The requirements regarding actual value and status displays
were addressed by installing the AOP30 Advanced Operator
Panel in the doors of the drive cabinet.
Coated PCBs and nickel-plated copper busbars were selected
as a result of the aggressive atmosphere with a high percentage
of H
2
S.
Since the availability of equipment is extremely important in the
paper industry, the option "memory card left" should also be
selected in order to reduce downtimes. The firmware and addi-
tional AOP text languages are stored on this card. Further,
parameter values can be additionally saved there and there is
a reserved memory range for offline long-time trace records.
The following options must be selected for this particular
application:
L05
(electronics power supply for connection to 24 V DC)
L11
(2Q field power section)
M08
(coated PCBs)
M10
(nickel-plated copper busbars)
S01
(memory card left)
Further, the following accessories are required:
AOP30 Advanced Operator Panel (6SL3055-0AA00-4CA4)
RS485 cable, 3 m long
The ordering data are as follows:
6RA8093-4KV62-0AA0-Z
L05+L11+M08+M10+S01
and
6SL3055-0AA00-4CA4
as well as
6RY1807-0AP00
© Siemens AG 2014