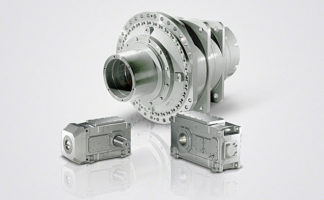
SINAMICS DCM
Engineering information
Notes for EMC-compliant drive installation
5/24
Siemens D 23.1 · 2014
5
■
Overview
(continued)
EMC-compliant drive installation (installation instructions)
General information
Not only are drives operated in a wide variety of environments,
but the electrical components used (controls and switched
mode power supplies, and so on) can also differ widely with re-
spect to interference immunity and interference emission levels,
meaning that all installation guidelines of any kind can offer is a
practical compromise. This is the reason that it is possible to
deviate from the EMC rules on a case-for-case basis provided
that individual measures are tested.
In order to ensure electromagnetic compatibility (EMC) in your
control cabinets in rugged electrical environments and adhere to
the standards required by the relevant legislating body, the EMC
rules listed below should be followed during the construction
and design stages.
Rules 1 to 10 are generally valid. Rules 11 to 15 must be followed
in order to fulfill interference emission standards.
Rules for EMC-compliant installation
Rule 1
All metal parts of the control cabinet are connected with one
another through a large surface area with a good electrical
connection (not paint on paint!). If required, contact or serrated
washers should be used. The cabinet door must be connected
to the cabinet using the shortest possible grounding straps (at
the top, center, and bottom).
Rule 2
Contactors, relays, solenoid valves, electromechanical operat-
ing hours counters, etc., in the cabinet and – where applicable –
in neighboring cabinets – must be provided with quenching
combination, e.g. RC elements, varistors, and diodes. The pro-
tective circuit must be directly connected to the particular coil.
Rule 3
Signal cables
1)
if at all possible, should only be routed at just
one level in the cabinet.
Rule 4
Unshielded cables in the same circuit (outgoing/incoming con-
ductors) must be twisted wherever possible, or the area between
them minimized, to prevent the unnecessary formation of frame
antennae.
Rule 5
Connect spare wires at both ends to the cabinet ground
(ground
2)
). This achieves an additional shielding effect.
Rule 6
Avoid unnecessary cable lengths. This keeps coupling
capacitances and inductances low.
Rule 7
Crosstalk is generally reduced, if cables are routed close to the
control cabinet ground. Therefore, do not route cables freely
around the cabinet, but route them as close as possible to the
cabinet enclosure or to the mounting plates. This also applies
to spare cables.
Rule 8
Signal and power cables must be physically separated (to
prevent coupling paths!). A minimum distance of 20 cm must
be observed.
If it is not possible to physically separate the encoder and motor
cables, the encoder cable must be decoupled either using a
partition or by routing it in a metal conduit. The partition or metal
conduit must be grounded at several points.
Rule 9
Ground the shields of digital signal cables at both ends (source
and destination), ensuring maximum contact area and good
conductivity. In the event of poor equipotential bonding between
the shield connections, run an additional equipotential bonding
conductor with a cross-section of at least 10 mm
2
parallel to the
shield for the purpose of reducing the shield current. Generally
speaking, the shields may also be connected to the cabinet
enclosure (ground) at several points. The shields can be con-
nected several times even outside the control cabinet.
Foil-type shields should be avoided, as they are at least 5 times
less effective than braided shields.
Rule 10
Shields for analog signal cables may be connected to ground at
both ends if the equipotential bonding is good (this must be
done through a large surface area with good conductivity!). It
can be assumed that equipotential bonding is good if all of the
metal parts are interconnected with one another through a good
electrical connection and the electronics components are sup-
plied from a single source.
Connecting shields at one end prevents low-frequency, capaci-
tive interference from being coupled in (e.g. 50 Hz hum). In this
case, the shield should be connected in the control cabinet;
whereby the shield can also be connected using a separate
wire.
Rule 11
Ensure that the radio interference suppression filter is located
close to the suspected source of interference. The filter must be
attached to the cabinet enclosure, mounting plate, etc., through
a large surface area. Incoming and outgoing cables must be
physically separated.
Rule 12
Radio interference suppression filters must be used in order to
conform to limit value class A1. Additional loads must be con-
nected upstream of the filter (line side).
The control used and the manner in which the rest of the control
cabinet is wired will determine whether an additional line filter
needs to be installed.
Rule 13
A commutating reactor must be included in the field circuit for
controlled field power supplies.
Rule 14
A commutating reactor must be included in the armature circuit
of the converter.
Rule 15
The motor cables do not have to be shielded. There must be a
clearance of at least 20 cm between the line supply feeder cable
and the motor cables (field, armature). If necessary, a separat-
ing metal partition should be used.
The cabinet design shown in the following diagram is intended
to help the user become familiar with EMC-critical parts. This ex-
ample does not claim to show all possible cabinet components
or design options.
Additional diagrams show details that are not immediately clear
in the overview diagram and which may also have an effect on
the resistance to interference/interference emission levels of the
cabinet as well as different shield connection techniques.
1)
Signal cables are defined as:
Digital signal cable:
Cables for pulse encoders,
Serial interfaces, e.g. PROFIBUS DP or
analog signal cable, e.g.
±
10 V setpoint cable.
2)
Generally speaking, "ground" refers to all metallic conductive parts that can
be connected to a protective conductor, such as the cabinet enclosure,
motor enclosure, or foundation ground etc.
© Siemens AG 2014