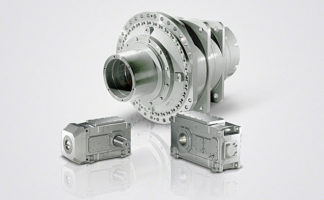
SINAMICS DCM
Engineering information
Notes for EMC-compliant drive installation
5/23
Siemens D 23.1 · 2014
5
■
Overview
(continued)
Four different categories are defined in EN 61800-3 Ed.2
depending on the installation site and the power of the drive:
Category C1:
Drive systems for rated voltages < 1000 V for
unrestricted use in the first environment.
Category C2:
Stationary drive systems for rated voltages
< 1000 V for use in the second environment. Use in the first
environment is possible if the drive system is marketed and
installed by qualified personnel. The warning information and
installation instructions supplied by the manufacturer must be
observed.
Category C3:
Drive systems for rated voltages < 1000 V for
exclusive use in the second environment.
Category C4:
Drive systems for rated voltages
≥
1000 V or for
rated currents
≥
400 A for use in complex systems in the second
environment.
The following diagram shows how the four categories are
assigned to the first and second environments:
Definition of categories C1 to C4
SINAMICS DC MASTER units are nearly always used in the
second environment (Categories C3 and C4).
Radio interference suppression filters and commutating reactors
are required whenever they are to be used in Category C2.
SINAMICS DC MASTER units conform to the interference
immunity requirements defined in EN 61800-3 for the second
environment, and thus also to the lower requirements in the
first environment.
Standard EN 55011
Some situations require compliance with standard EN 55011.
This defines limit values for interference emissions in industrial
and residential environments. The values that are measured are
conducted interference at the line supply connection as inter-
ference voltage, and electromagnetically radiated interference
as radio interference, under standardized conditions.
The standard defines limit values "A1" and "B1" which, for inter-
ference voltage, apply to the 150 kHz – 30 MHz range and, for
radio interference, the 30 MHz – 2 GHz range. Since
SINAMICS DC MASTER converter units are used in industrial
applications, they are subject to the limit value "A1"; in order to
achieve limit value "A1", the SINAMICS DC MASTER units must
be provided with external radio interference suppression filters
and commutating reactors.
SINAMICS DC MASTER, industrial applications
Industrial applications demand that units demonstrate an ex-
tremely high level of interference immunity, but by contrast place
very low requirements on them in terms of interference emission
levels.
SINAMICS DC MASTER converter units are components of an
electrical drive, such as contactors and switches. Qualified
personnel must integrate them into a drive system which, as an
absolute minimum, consists of the converter unit, motor cables,
and motor. Commutating reactors and fuses are also required in
most cases. Therefore, whether or not a limit value is adhered to
is determined by the components being installed correctly.
Limiting interference emission levels in line with limit value "A1"
requires not only the converter unit itself, but also the radio inter-
ference suppression filter assigned to it and the commutating re-
actor, at the very least. Without a radio interference suppression
filter, the interference emission level of SINAMICS DC MASTER
converter units exceeds limit value "A1" of EN 55011.
If the drive forms part of a plant or system, it does not initially
need to fulfill any interference emission requirements. However,
EMC legislation does stipulate that the plant or system as a
whole must be electromagnetically compatible with its environ-
ment.
If all the control components in the plant or system (such as
PLCs) demonstrate a level of interference immunity that is suit-
able for industrial applications, then it is not necessary for every
drive to adhere to limit value "A1".
Non-grounded line supplies
Non-grounded line supplies (IT line supplies) are used in some
branches of industry in order to increase the availability of the
plant. In the event of a ground fault, no fault current flows and the
plant can continue with production. However, in conjunction with
radio interference suppression filters, in the case of a fault, a
fault current flows, which can cause the drives to shut down or
possibly even destroy the radio interference suppression filter.
This is the reason that the product standard does not define any
limit values for these types of line supplies. From an economics
perspective, any necessary EMC conformance measures
should be taken on the grounded primary side of the supply
transformer.
EMC planning
If two units are not electromagnetically compatible, you can
reduce the interference emission level of the source of inter-
ference or increase the interference immunity of the potentially
susceptible equipment.
Sources of interference are generally power electronics units
with high power consumption. Reducing their interference
emission levels requires complex filters. Potentially susceptible
equipment usually refers to controlgear and sensors, including
their evaluation circuit. Lower costs are involved with increasing
the interference immunity of units with lower power ratings. This
means, that from an economics perspective, increasing the
interference immunity is generally a more favorable option for
industrial applications than reducing the interference emission
level. For example, to maintain limit value class A1 of EN 55011,
the radio interference voltage at the line supply connection point
between 150 and 500 kHz can be a maximum of 79 dB (
µ
V) and
between 500 kHz and 30 MHz, a maximum of 73 dB (
µ
V) (9 or
4.5 mV).
In industrial applications, EMC between units should be based
on a carefully-balanced combination of the interference emis-
sion and interference immunity levels.
The most cost-effective measure that can be put in place to
achieve EMC conformance is to physically separate sources of
interference and potentially susceptible equipment – provided
that you have taken this option into account during the planning
stage of your machine/plant. In the first instance, it is necessary to
determine whether each unit used is a potential source of inter-
ference or potentially susceptible equipment. Within this context,
converter units and contactors, for example, can be counted as
sources of interference. While examples of potentially susceptible
equipment include PLCs, encoders and sensors.
The components in the control cabinet (sources of interference
and potentially susceptible equipment) must be physically
separated, by means of partition plates if necessary, or by
installing them in metal enclosures.
G_D213_EN_00009a
First
environment
Second
environment
C1
C2
C4
C3
© Siemens AG 2014