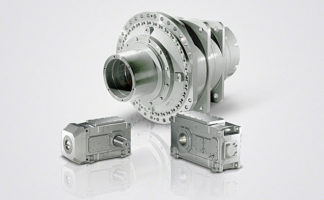
SINAMICS DCM
Engineering information
Dynamic overload capability
5/2
Siemens D 23.1 · 2014
5
■
Overview
Determining the dynamic overload capability
Function overview
The rated DC current specified on the unit rating plate (maxi-
mum permissible continuous DC current) may be exceeded in
operation. The extent to which this value is exceeded and how
long this lasts are subject to certain limits, which are explained
in more detail in the following.
The absolute upper limit for the value of the overload currents is
1.8x the rated DC current. The maximum overload duration de-
pends on the time characteristic of the overload current as well
as on the load history of the unit and also depends on the
specific unit.
Each overload must be preceded by an underload (load phase
with load current < rated DC current). Once the maximum per-
missible overload duration has elapsed, the load current must
return to at least an absolute value
≤
the rated DC current.
The dynamic overload duration is made possible by thermally
monitoring the power section (
I
2
t
monitoring).
I
2
t
monitoring
uses the time characteristic of the actual load current to calcu-
late the time characteristic of a substitute value for the increase
of the depletion layer temperature of the thyristors above the
ambient temperature. In this case, unit-specific properties (e.g.
thermal resistances and time constants) are incorporated in the
calculation. When the converter unit is switched on, the calcula-
tion process starts with the initial values that were determined
before the shutdown/line supply failure. The environmental con-
ditions (ambient temperature and installation altitude) must be
taken into account when setting a parameter.
I
2
t
monitoring responds when the calculated substitute depletion
layer temperature rise exceeds the permissible value. Two
alternatives can be parameterized as response:
•
Alarm with a reduction of the armature current setpoint to
the rated DC current or
•
Fault with unit shutdown
I
2
t
monitoring can be disabled. In this case, the armature current
is limited to the rated DC current.
Configuring for the dynamic overload capability
The configuring sheets contain the following information:
•
The maximum overload duration
t
an
when starting with a cold
power section and specified, constant overload,
•
The maximum zero current interval
t
ab
(maximum cooling
down time) until the "cold" thermal state of the power section
is reached, and
•
Fields of limiting characteristic for determining the overload
capability during thermally stabilized, intermittent operation
with overload (periodic duty cycles)
Technical support personnel from the local Siemens office can
provide assistance with the selection of units for duty cycles
involving multiple duty stages and cycle times in excess of
300 s.
Remark: The power section is considered to be "cold" if the
calculated substitute depletion layer temperature rise is less
than 5 % of its maximum permissible value. This state can be
queried using a binary assignable output.
Structure of the fields of limiting characteristics for intermittent
operation with overload
The fields of limiting characteristics refer to a duty cycle of the
intermittent overload operation with a total duration (time period)
of 300 s. Such a duty cycle comprises two time sections – the
base-load duration (armature current actual value
≤
rated DC
current) and the overload duration (armature current actual
value
≥
rated DC current).
Each limiting characteristic represents a unit-specific maximum
base-load current for a specific overload factor (limiting base-
load current, specified as a % of the rated DC current) over the
minimum base-load duration (limiting base-load duration). For
the remaining duration of the duty cycle, the maximum permissi-
ble overload current is determined by the overload factor. If no
limiting characteristic has been specified for the required over-
load factor, then it will be subject to the limiting characteristic for
the next highest overload factor.
The fields of limiting characteristics are valid for a duty cycle of
300 s. Using basic calculation algorithms, duty cycles can be
configured with duty cycle durations of longer than or shorter
than 300 s. This will now be shown using two basic tasks.
Characteristic example for basic tasks 1 and 2
300
200
250
100
150
50
0
50
40
30
20
10
0
100
%
90
80
70
60
1438
906
631
455
333
123
Overload with x-times
rated DC current
(s)
an
(s) = 2193
ab
Example of basic task 2
Example of basic task 1
Overload duration in s for 300 s cycle duration
Base-load current as a % of the rated DC current
G_D023_EN_00022
t
t
x=1.1
x=1.2
x=1.3
x=1.4
x=1.5
x=1.8
x=1.1
x=1.2
x=1.3
x=1.4
x=1.5
x=1.8
© Siemens AG 2014