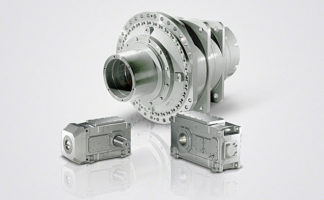
ROBICON Perfect Harmony
Liquid-cooled drives
5
5/5
Siemens D 16.2 – 2012
Mode of operation (continued)
Drive input protection
ROBICON Perfect Harmony utilizes software functions to
detect abnormal conditions due to an internal drive failure
and thus provides protection to the drive. Below you find a
description of some routines that are implemented in NXGII
control for drive protection.
Faults within the drive can be categorized into two types –
“low impedance” (with high current) and “high impedance”
(with low current) faults. A “low impedance” fault within the
drive or the secondary side of the transformer would result
in a significant reactive current on the primary side. The
“one cycle protection” (or excessive input reactive current
detection) is implemented to detect such types of faults. A
“high impedance” fault within the drive would result in low
current that is difficult to detect on the primary side of the
transformer but will result in measurable losses that can
be used to sense the condition. The “excessive drive losses
protection” allows the detection of such faults.
The level of currents detected by these functions cannot be
easily detected and may be insufficient to activate the main
primary protection. Hence the fault signals issued by these
routines should be used with suitable interlocking, via a relay
output and/or serial communication, to disconnect medium-
voltage from the drive input.
One cycle protection
(or excessive input reactive current detection)
NXGII control utilizes the reactive component of the drive
input current to determine whether a “low impedance” fault
on the secondary side of the transformer has occurred. For
example, a short-circuit in one of the secondary windings
will result in poor power factor on the high-voltage side of
the transformer. A software model of the transformer is used
to predict the reactive component of primary current based
on the known load. An alarm and trip are generated when
the actual reactive current exceeds this prediction based on
an inverse time curve. Further in formation on this curve and
the time to trip is provided below. This event will normally
cause the input disconnect device to open. The one cycle
protection is defeated during the first 0.25 seconds after
primary voltage is applied, to allow transformer saturation
inrush to decay.
Excessive drive losses protection
The excessive drive losses protection uses drive losses to
protect the drive against “high impedance” fault conditions.
The drive losses are calculated as the difference between the
measured input and output powers, and compared against
reference losses. Once the threshold is exceeded, a fault is
issued and the drive trips based on an inverse time curve.
During the idle state if the drive losses exceeds the idle
threshold by 1 to 2 % the control will issue a command to
open the input breaker within 250 ms. Such a fast response
will greatly reduce the adverse effect of a “high impedance”
fault on the drive system.
Speed and torque control
Feature
V/Hz
control
Open-loop
vector
control
Closed-loop
vector
control
Speed range (for 100%
holding torque and 150%
starting torque)
40:1
100:1
200:1
Torque regulation
(% of rated)
n/a
± 2 %
± 2 %
Torque linearity
(% of rated)
n/a
± 5 %
< ± 5 %
Torque response
1)
n/a
> 750 rad/s
> 750 rad/s
Speed regulation
(% of rated)
Motor slip
± 0.5 %
2)
± 0.1 %
3)
Speed response
4)
20 rad/s
20 rad/s
> 20 rad/s
5)
Torque pulsation
(% of rated) without
over-modulation
6)
< 1.0 %
< 1.0 %
< 1.0 %
Torque pulsation
(% of rated) with
over-modulation
6)
< 3.5 %
< 3.5 %
< 3.5 %
Note:
Applications that require lower than 1% speed
operation under high load torque should use the CLVC
mode. In such cases it is preferable to select a motor that
has high full-load slip (> 1.0 %) and high breakdown torque.
1)
Torque response values are valid for drive without an output filter.
Tuning may be required to achieve these values.
2
) Approx. 0.3 % speed error is typical. Worst-case speed error is equal to
approximately 30 % of rated motor slip.
3
)
0.1 % can be achieved with a 1024 PPR encoder. Speed accuracy
depends on the encoder PPR.
4
)
Speed response numbers apply as long as torque limit is not reached.
5
)
Testing is required to determine exact value.
6
)
ROBICON Perfect Harmony drives when not operated in over-
modulation, will have torque pulsation amplitudes of less than 1%
as listed in the above table. For a drive operating in over-modulation
the torque pulsation is higher at the 6th harmonic frequency
(i.e. 6f component) which is introduced only in the speed range of 95
to 100 % of rated. Torque pulsations at all other frequencies are under
1 % of rated. Refer to section Output Voltage Characteristics (next
page) for more information on the cell voltage and drive output
voltage ratings that will operate with over-modulation.
Engineering Information