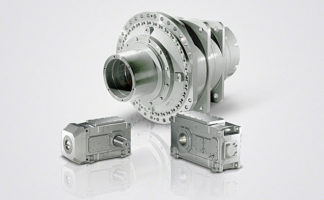
ROBICON Perfect Harmony
Liquid-cooled drives
5/4
Siemens D 16.2 – 2012
5
Mode of operation
Control features
The following table provides a summary of the performance
offered by the ROBICON Perfect Harmony drives with
NXGII control.
Overview of control features
Feature
Description
Output frequency
0 ... 300 Hz
1)
; above 167 Hz, current derating is required
Modulation
Multi-level PWM
Ride-through
• Medium-voltage ride-through:
minimum 5 cycles
• Control power ride-through with UPS:
minimum 5 cycles
Spinning load
• Instantaneous mode: allows fast bypass
• Frequency scan mode: performed after residual motor voltage has collapsed
Induction motor control
• V/Hz for parallel motors (VHz)
• Open-loop vector control for induction motors (OLVC)
• Closed-loop vector control for induction motors (CLVC)
Synchronous motor control
• Open-loop vector control for synchronous motors (OSMC)
• Closed-loop vector control for synchronous motors (CSMC)
Emergency Stop category
Emergency stop category 0 is set as standard for an uncontrolled shutdown.
The function includes voltage disconnection of the drive output by opening the
circuit-breaker.
Consequently the motor coasts down.
Energy saver
Single parameter driven (for induction motors only)
Braking
2)
• Inverse speed (max. braking torque is approx. 0.25 % at full speed and increases as speed is reduced)
• Regenerative Braking
3
)
• Dynamic Braking
4
)
Auto tuning
Available for induction motors as long as the drive rating is higher than 67 % of the motor
Advanced Cell Bypass
(option U11)
250 ms downtime with redundant cells; without redundant cells, the downtime depends on the
motor open circuit time constant
Synchronous transfer
(option L29)
Closed synchronous transfer available for induction and synchronous motors
5)
Voltage minimum boost
Not implemented; as an alternate, automatic stator resistance compensation is available in
OLVC/CLVC/OSMC/ CSMC control modes (also see description for flux attenuation shaping)
Flux attenuation shaping
Not implemented; a simple (single parameter function) implementation is available
Zero speed control
Not implemented
Engineering Information
1)
Although 0 Hz can be produced by the drive, torque production is limited.
2
)
Note: 4Q cells are qualified and released for braking (intermittent) regeneration applications. Please, contact the factory or your local Siemens sales
representatives for more details.
3
)
For continuous power regeneration applications, please, contact the factory or your local Siemens sales representatives for more details.
4
)
For Dynamic Braking, please, contact the factory or your local Siemens sales representatives for more details.
5
)
Synchronous transfer applications with synchronous motors would require a PLC to manage the exciter control.