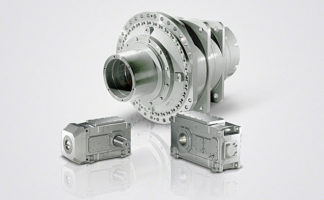
ROBICON Perfect Harmony
Liquid-cooled drives
2
2/9
Siemens D 16.2 – 2012
Drive Selection Criteria
The following tables help you to select the right converter
type and give an overview of the corresponding motor data
and order numbers. The tables are organized according to
the motor voltages. For the complete technical data of the
listed converter types refer to Chapter 3.
In order to select the right ROBICON Perfect Harmony drive,
please take into consideration the following steps:
Step 1 – Choosing the right cell size
1.1 Determine the maximum continuous motor current,
temporary overload not included:
• Use the motor full load line current (FLA) if
available or use the following formula to calculate
motor current
I
.
I motor
where,
P
motor
__kW
=
shaft output (in kW)
V
motor
=
motor voltage
PF
motor
=
motor power factor = (cos
φ
motor)
h
motor
=
motor efficiency
(keeping in mind: motor service factor if utilized and/or
overload requirements)
• If the motor power factor (
PFmotor
) and efficiency
at full load are not known then use the following
default values:
–
PF
motor
= 0.88
–
h
motor
= 0.96
• Factor in the motor service factor (SF) if the application
will make use of it under long term operation. You do so
by multiplying the given/calculated current (from step
1.1) by the motor SF.
1.2
Determine the minimum continuous cell current rating:
• If the drive is intended to operate within nominal
parameters, the maximum continuous motor current
will be the minimum continuous cell current rating.
1.3
Factor in any overload requirements:
• For the cell chosen on the previous paragraph,
make sure it can handle the application overload
requirements by checking overload capabilities
(see page 2/8).
• If the overload requirements exceed the capabilities
of the chosen cell then the next larger cell size must
be selected.
Step 2 – Choosing the right transformer
2.1
The ROBICON Perfect Harmony transformer rating is
based on the motor shaft horsepower:
• If the drive is intended to operate within nominal
parameters and without added redundant cells, the
maximum continuous motor horsepower (hp) will be
used to rate the transformer using a straight formula:
1 transformer kVA per each motor hp
• The above rule is followed regardless of motor type.
2.2
The transformer is designed to support the temporary
overloads associated with the cells it feeds. If those
levels are exceeded by the application requirements,
please contact the factory or your local Siemens
sales representative.
Note:
Please contact the factory or your local Siemens sales
representative for derating calculations, if the drive is
intended to operate outside the nominal conditions
such as:
• High ambient temperatures
• High altitude installations
• Very low continuous operating frequencies at high current
• High frequency operation for high speed motors
Selection and Ordering Data