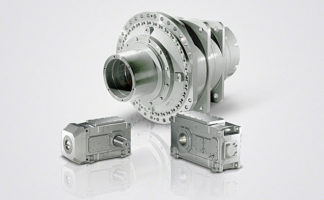
ROBICON Perfect Harmony
Liquid-cooled drives
2
2/6
Siemens D 16.2 – 2012
Design (continued)
Siemens calls this approach Neutral Shift.
1)
This approach is
equivalent to introducing a zero-sequence component into
the voltage command vectors for the cells. In the figure below,
the full remaining 87% of functional cells are in use, and 80%
of the original voltage is available. The phase angles of the
cell voltages have been adjusted so that phase A is displaced
from phase B and from phase C by 132.5°, instead of the
normal 120°.
Figure 2.7 Drive output rebalanced by adjusting phase angles
(Neutral Shift).
Pre-charge operation for WCIII drive
With the use of film capacitors, it has become necessary
to control the inrush current into the cell modules used by
the ROBICON Perfect Harmony WCIII drive. By controlling
the inrush current, excessive currents and voltage overshoot
within the cell are eliminated. A pre-charge system is used
to control the inrush currents seen by the cells. In addition,
the pre-charge circuit may be optionally used as a pre-
magnetization circuit to limit transformer inrush currents.
The pre-charge circuit consists of a collection of capacitors,
resistors, and contactors mounted within the Fuse/Pre-charge/
Control (FPC) cabinet on the input section of the drive.
(Refer to Figure 2.8). On the left is the low voltage pre-charge
source coming in through the pre-charge circuit breaker into
the pre-charge circuit. On the right side is the connection
from the pre-charge circuit to a set of secondary windings
of the input transformer. Voltage during pre-charge is
monitored through the input attenuators on the primary
side of the transformer. When pre-charge is complete, a
contactor connects the medium voltage source to the
transformer primary winding.
Note: During pre-charge, medium voltage is present on the
primary side of the input transformer even though the MV
Contactor is not closed.
For more Pre-Charge information please contact the factory
or your local Siemens sales representative.
Figure 2.8 Pre-charge component connection diagram.
A
B
C
95°
A3
A2
A1
B1
B1
C1
B5
B4
C4
B3
C3
B2
C2
C5
15 module drive after
bypass of 2 modules
in phase A only
and adjustment of
phase angles.
87 % of the modules
are in use.
80 % of full voltage
is available.
132.5°
132.5°
V
AC
V
BA
V
CB
G_D015_EN_00008
Introduction
1)
Siemens patented technology; Patent number 5,986,909.
Input power
3-phase AC
480 to 600 V
3-phase source
Transformer with
12 1,375 V isolated
secondaries
Input power
3-phase AC
M1
V1
Pre-charge current
Pre-charge winding
Lead 22.5"
Lead 22.5"
Lead 22.5"
Lead 7.5"
Lead 7.5"
Lead 7.5"
Lag 7.5"
Lag 7.5"
Lag 7.5"
Lag 22.5"
Lag 22.5"
Lag 22.5"
Pre-charge voltage
Induction
Motor
Ce l
A4
Ce l
B4
Ce l
C4
Ce l
A3
Ce l
B3
Ce l
C3
Ce l
A2
Ce l
B2
Ce l
C2
Ce l
A1
Ce l
B1
Ce l
C1
Pre-charge circuit