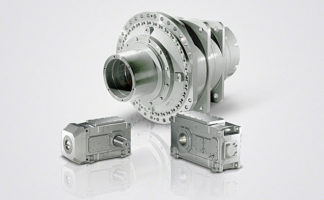
ROBICON Perfect Harmony
Liquid-cooled drives
2
2/5
Siemens D 16.2 – 2012
Design (continued)
Advanced cell bypass
The ROBICON Perfect Harmony is designed to withstand
failures that would overwhelm conventional drives
because redundancy options are added into the system.
The patented, cell-based configuration maximizes uptime
and simplifies modifications.
Through a redundant bypass control that is completely
separated from each power cell, the ROBICON Perfect
Harmony ensures automatic bypass of a failed power cell
in less than 250 ms.
Since the cells in each phase of a ROBICON Perfect Harmony
drive are in series, bypassing a cell has no effect on the
current capability of the drive, but the voltage capability
will be reduced. Usually the required motor voltage is
roughly proportional to speed, so that the maximum
speed at which the drive can fulfill the application
requirements will also be reduced.
Therefore, it is important to maximize the motor voltage
available after one or more cells have been bypassed. The
following figures illustrate the voltage available from a
ROBICON Perfect Harmony drive, where the cells, represented
by circles, are shown as simple voltage sources. Figure 2.4
shows a 15-cell drive in which no cells are bypassed. With
100% of the cells in use, 100% of the original voltage is
available. The voltage commands to the three phase groups
of cells will have phase A displaced from phase B by 120°,
and from phase C by 120°.
Figure 2.4 Simplified diagram of a 15 cell drive
When two cells are bypassed in phase A, the output voltage
will tend to become unbalanced, as illustrated in Figure 2.5.
Figure 2.5 Drive output with 2 cells bypassed in phase A
One possible remedy is to bypass an equal number of cells
in all three phases, even though some may not have faulted.
Figure 2.6 illustrates this approach. Obviously, this method
prevents unbalance but sacrifices possible voltage capability.
In this figure, 87% of the cells are functional, but only 60%
are in use, and only 60% of full voltage is available.
Figure 2.6 Drive output rebalanced by bypassing functional cells
A better approach is illustrated in figure 2.7. This method takes
advantage of the fact that the star-point of the cells is floating,
and is not connected to the neutral of the motor. Therefore
the star-point can be shifted away from the motor neutral, and
the phase angles of the cell voltages can be adjusted, so that
a balanced set of motor voltages is obtained even though the
cell group voltages are not balanced.
C4
B4
C5
B3
C2
B2
C1
A1
A2
A3
A4
A5
B1
C5
B5
B
A
N
C
120°
15 module drive with
no modules bypassed.
100 % of the modules
are in use.
100 % of full voltage
is available.
V
AC
V
BA
V
CB
G_D015_EN_00013
C4
B4
C3
B3
C2
B2
C1
A1
A2
A3
B1
C5
B5
B
A
N
C
120°
15 module drive after
bypass of 2 modules
in phase A.
87 % of the modules
are in use, but the
output voltage is
available unbalanced.
V
AC
V
BA
V
CB
G_D015_EN_00014
A2
A1
A3
B1
C1
B2
C2
B3
C3
A
B
N
C
120°
15 module drive after
bypass of 2 modules
in all phases.
Balance is restored.
87 % of the modules
are OK, but only
60 % are in use.
60 % of full voltage
is available.
V
AC
V
BA
V
CB
G_D015_EN_00007
Introduction