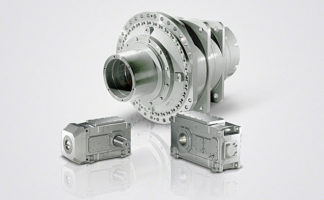
1/64
Siemens D 83.1 · 2016
1
Introduction
General technical specifications
Brakes and brake motors
■
Overview
(continued)
Basis for the calculation
A brake is designed mainly in accordance with the required
braking torque
T
req
.
The masses to be braked (moments of inertia), relative speeds,
braking times and the switching frequencies must be included
in the calculations. The boundary conditions, such as ambient
temperature, air humidity, dust accumulation and mounting
position must be known. In the case of extreme/critical operating
conditions, the manufacturer should be consulted.
Dimensioning must be in accordance with VDI guideline 2241.
The friction surfaces must be kept free of grease and oil at all
times.
Safety factor
In order to ensure that mechanical transmission is reliable even
under extreme operating conditions, the calculated braking
torque should include the safety factor K which must be selected
in accordance with the operating conditions.
Load types
In practice, the following main types of load occur:
T
req
=
T
a
· K +
T
B
Dynamic and static loading
Most application cases involve a mixture of loads, because a
dynamic load is added to a static load torque.
T
req
= (
T
a
±
T
L
) · K +
T
B
+
T
L
is used, for example, when lowering a load
-
T
L
is used for normal braking
Rough determination of the required braking torque or
frame size
If only the drive power to be transferred is known, the required
torque or braking torque can be determined as follows:
Thermal load capacity
If high switching frequencies and increased friction energy per
switching cycle are expected, thermal recalculation of the brake
is recommended.
The friction energy per switching cycle is calculated as follows:
-
T
L
is used, for example, when lowering a load
+
T
L
is used for normal braking
The admissible friction energy per switching cycle for a known
switching frequency can be obtained from the following
diagram. For a known friction energy per switching cycle, the
admissible switching frequency can similarly be obtained from
this diagram.
Abbreviations and definitions used
P
Drive power in kW
T
B
Characteristic torque for the brake in Nm
T
L
Load torque in Nm
T
req
Required braking torque in Nm
T
a
Deceleration torque in Nm
n
0
Initial relative speed of the brake in rpm
J
L
Moment of inertia of all drive components referred
to the shaft to be braked in kgm
2
t
1
Application time,
t
1
=
t
11
+
t
12
in s
t
2
Disengaging time (time from the start of torque removal
until the value 0.1
T
B
is reached) in s
t
3
Sliding (time during which a relative movement occurs
between the input and the output with the brake
engaged) in s. This time depends on the delay required
by the application case e.g. switching frequency
t
11
Responding delay on engaging (time from voltage
switch-off up to the moment when the torque begins
to rise) in s
t
12
Time taken for the braking torque to rise in s
K
Safety factor
Q
Calculated switching energy per switching cycle in J
Q
adm
Max. admissible switching energy per switching cycle
in J
S
n
Switching frequency, i.e. the number of braking
operations distributed evenly over the time unit in h
-1
T
req
= 9550 ——
×
K
≤ T
B
P
∆n
0
Q =
———— × ————
J
L
+ ∆n²
182.5
T
B
T
B
+ T
L
© Siemens AG 2016