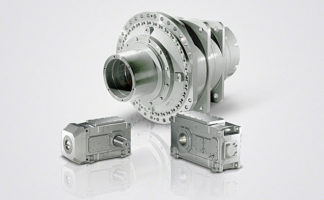
1/59
Siemens D 83.1 · 2016
1
Introduction
General technical specifications
Brakes and brake motors
■
Overview
(continued)
The surface-cooled brake motors are equipped with a quiescent
current-operated (fail-safe) single-disk spring-operated brake
with two asbestos-free brake pads. The bearing plate at the non-
drive end is specially shaped and it is made of cast-iron in every
motor. Refer to the table for the size of the bearings. Otherwise,
in terms of their mechanical design, the brake motors
correspond to the surface-cooled three-phase motors.
The brakes and fans of the brake motors are suitable for both
directions of rotation. The degree of protection for the brake
motors is IP55. Other degrees of protection are possible on
request.
If it is necessary to rotate the shaft in the zero current state, the
brake can be specially ordered with a manual release. All brakes
feature torque adjustment.
Single-disk spring-operated brake
Design
Single-disk spring-operated brakes are fail-safe brakes with
2 frictional surfaces in which an electromagnetic field is used to
release the brake which is applied using spring force. The
spring-operated brake brakes in the zero current state and
releases when current is flowing.
Special characteristics of the single-disk spring-operated brake:
•
Braking in accordance with DIN VDE 0580
"Electromagnetic devices and components –
General specifications"
•
Holding brake with spring-loaded operation
•
Microswitch for air gap monitoring as an option
(brake size 12 and above)
•
Braking torque is active in zero current state
(fail-safe brake)
•
Rugged and simple design
•
High level of operational reliability due to long service life
•
Brakes are designed for temperature class F
•
Large operating air gap makes automatic readjustment
superfluous
•
Under conditions of extremely high wear, the operating air gap
is easily adjusted
•
Braking torque can be adjusted between 100 % and
approximately 60 %
•
Manual release with automatic return
•
Brakes are corrosion-protected, asbestos-free friction pads
•
The brakes are designed for 100 % duty ratio
•
The brakes will operate in any position
The standard voltages for the brake coils are: 24 V, 103 V, 180 V,
205 V +5 to 10 %. For the relationship between brake control
voltage, rectifier type and brake coil voltage, see the section
"Circuit diagrams”.
Brakes with special requirements
Special brakes can be ordered for particular environments and
requirements.
Other versions are available for:
•
Ship design, e.g. acc. to DNV GL, ABS, etc.
•
Highly corrosive environments (e.g. offshore, onshore)
•
Special customer requirements
- in conjunction with special paint systems
(V11, V12, W05)
- in conjunction with high degrees of protection (IP65, IP66)
- in conjunction with a second shaft extension or forced
ventilation
-
in conjunction with explosion protection for gas zone 1/2 and
dust zone 21/21
- in conjunction with increased ambient air temperatures
Electrical connection
In the terminal box, apart from the motor connection terminals,
there is also a bridge rectifier for the standard 230-V brake
control voltage. For higher brake control voltages, either a half-
wave rectifier with zero diodes can be installed or connection
can be performed via an intermediate transformer that is,
however, not included in the scope of supply. For cases in which
the motor operating voltage does not comply with the brake
control voltage, a separate brake control voltage must be
supplied via an additional contact.
© Siemens AG 2016