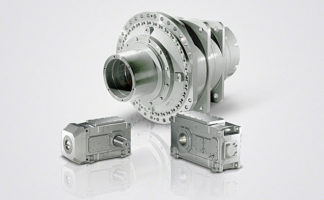
1/23
Siemens D 83.1 · 2016
1
Introduction
General technical specifications
Motor protection
■
Overview
In the standard version, the motor is designed without motor
protection. The order variants for motor protection are coded by
means of the selected options.
A distinction is made between current-dependent and motor
temperature-dependent protection devices.
Current dependent protection devices
Fuses are only used to protect line cables in the event of a short-
circuit. They are not suitable for overload protection of the motor.
The motors are usually protected by thermally delayed overload
protection devices (circuit breakers for motor protection or
overload relays). This protection is current-dependent and is
particularly effective in the case of a locked rotor.
For standard duty with short start-up times and starting currents
not too excessive and for low numbers of switching operations,
motor protection switches provide adequate protection.
Motor protection switches are not suitable for heavy starting duty
or large numbers of switching operations. Differences in the
thermal time constants for the protection equipment and the
motor result in unnecessary early tripping when the protection
switch is set to rated current.
Motor temperature dependent protection devices
Temperature detectors installed in the motor winding are
suitable protection devices in the case of slowly rising motor
temperature.
The most comprehensive protection against thermal
overloading of the motor is provided by PTC thermistors
(thermistor motor protection) installed in the motor winding. The
temperature of the winding can be accurately monitored thanks
to its low heating capacity and the excellent heat contact with
the winding. When a limit temperature is reached (rated tripping
temperature), the PTC thermistors undergo a step change in
resistance. This is evaluated by a tripping unit and can be used
to open auxiliary circuits. The PTC thermistors themselves
cannot be subjected to high currents and voltages. This would
result in destruction of the semiconductor. The switching
hysteresis of the PTC thermistor and tripping unit is low, which
supports fast restarting of the drive. Motors with this type of
protection are recommended for heavy duty starting, switching
duty, extreme changes in load, high ambient temperatures or
fluctuating supply systems.
Option A11
Motor protection through PTC thermistors with 3 embedded
temperature sensors for tripping. In the terminal box, 2 auxiliary
terminals are required.
Two sets of three temperature sensors are used if a warning is
required before the motor is shut down (tripped). The warning is
normally set to 10 K below the tripping temperature.
Option A12
Motor protection with PTC thermistors with 6 embedded
temperature sensors for warning and tripping. In the terminal
box, 4 auxiliary terminals are required.
In order to achieve full thermal protection it is necessary to
combine a thermally delayed overcurrent release and a
PTC thermistor. For full motor protection implemented only
with PTC thermistors, please inquire.
Motor temperature detection with converter operation
PTC sensor
The PTC thermistor is a temperature-dependent component.
In the region of the rated response temperature, the resistance
of the PTC increases very steeply.
PTC sensor characteristic
Option A15 or A16
For motors designed with explosion protection, the PTC sensors
must be tested in the installed state for correct operation
(TMS tests). For this test, the stator winding is heated to the
tripping temperature. The option of a PTC sensor including
TMS test can be ordered using Option
A15
(3 PTCs for tripping)
and
A16
(6 PTCs for prewarning/tripping).
10
4
10
3
10
2
10
1
T
KL
lg R
KL
Ω
G_D081_XX_00376
-20 °C
25 °C
T
NAT
-20 K
T
NAT
-5 K
T
NAT
+5 K
T
NAT
+15 K
T
NAT
© Siemens AG 2016