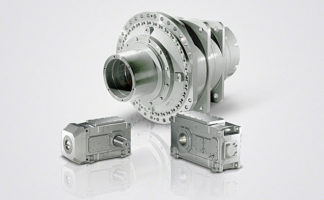
1/18
Siemens D 83.1 · 2016
1
Introduction
General technical specifications
Paint finishes
■
Overview
++
Long-term resistance
+
Good resistance
0
Limited resistance
–
Temporary resistance
– –
Not resistant
Order code
W10
can be used to order an internal coating in the
color RAL 7032 (pebble gray). This internal coating is included
in the case of paint systems N14 (not N14A), Z21, Z05 and S14.
The maximum corrosiveness category of this paint finish is
C3
high
.
Additional identification code
–Z
with order code
Standard
V09
V10 (W14)
V11
–
W15
K24
LOHER paint finish
System N04
System N08
System N14/J08
(paint finish
System N14A)
System Z21/J08
System S14 –
ETO option
(Engineer To
Order) without
order code
Special prime
coat system Z05
with internal cor-
rosion protec-
tion system J08
System
G04
Use
Use:
Standard
paint finish,
indoor instal-
lation,
standard for
1PS0, 1PS1
Outdoor
climate, tropi-
cal climate,
humid indoor
climate,
standard for
1PS4, 1PS5
Tropical climate,
humid indoor cli-
mate, VIK standard
paint finish, incl. J08
(N14A without J08)
highly aggressive
chemicals, decon-
tamination capabil-
ity, ships, onshore
Offshore, drilling
platforms, cus-
tomer request,
incl. J08/optional
(
V19
) with layer
thickness 275 μm
complies with
C5-M
high
Special under-
water offshore
paint approved
according to
NORSOK M-501
Coating System
1B
Customer
request
(top coat from
customer),
incl. J08
Customer
request
(top coat
from cus-
tomer)
Max. corrosiveness category/expected protection lifetime in accordance with EN ISO 12944 – see next page
Internal
–
C3
high
C5-M
low
C5-M
mid
C5-M
high
–
Im 1h
External
C3
mid
C3
mid
C5-I
mid
C5-M
low
C5-M
high
–
Im 1h
Layer thickness
μm
40
80
140
210
310
50
40
Resistance
Climate groups
acc. to EN 60721-3
Moderate
Worldwide
Worldwide
Worldwide
Worldwide
1)
1)
Condensation climate
acc. to KFW DIN 50017
+
+
++
++
++
+
+
Sulfur dioxide acc. to
EN ISO 6988
0
+
+/++
++
++
+
0
Saltwater according to
DIN 53167
0
+
+/++
++
+/++
+
0
Resistance according to EN ISO 2812-1
Ammonia ~10 %
+
++
++
++
++
+
+
Mineral oil, grease, solvent,
benzene/ benzol, alcohol
+
++
++
++
++
++
+
Sulfuric acid 10 %
0
+
++
++
+
+
0
Sulfuric acid 50 %
–
0
+
+
0
0
–
Bicarbonate of soda 10 %
0
+
++
++
+
+
–
Bicarbonate of soda 40 %
–
0
++
++
+
+
– –
Hydrochloric acid 37 %
0
0
+
+
–
–
–
Temperature range
-40 … +130 °C (temporarily -60 … +150 °C, at +180 °C possible slight discoloration)
Humidity
90 %
100 %
100 %
90 %
90 %
Ability to be painted
Good within 1 week, afterwards sanding down is necessary
Very good
Very good
Adhesion acc. to EN ISO 2409
Characteristic value Gt 1
Pre-treatment of parts
All parts cleaned and degreased, steel and cast-iron parts sandblasted.
Drying
All layers oven dried.
Colors
Standard
Standard RAL 7030 (stone gray)
RAL 7030
Gray
2)
RAL 7032
(pebble
gray)
Available colors
3)
RAL 1004, 1018, 2004, 5009, 5010, 5012, 5015, 5018, 6002, 6003, 6011, 7000, 7011,
7031, 7032, 7036, 7038, 9010, other colors are available on request
–
Surface treatment of unpainted parts, shaft extension and flange
Coated with special rust-protection oil that repells water and palm sweat
Miscellaneous
Abrasion-resistant, elastic, scratch-resistant, shock-proof, totally light resistant, physiologically harmless
1)
The corrosion class is produced by the customer using the additional paint
system.
2)
Color non-compliant with RAL.
3)
Colors with poor coverage, e.g. white or yellow, are not implemented in
N04, but instead with a greater layer thickness (e.g. N08).
© Siemens AG 2016