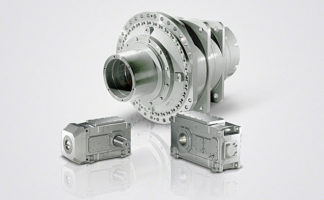
3/78
Siemens IC 10 · 2017
Power Contactors for Switching Motors
Accessories and Spare Parts for SIRIUS 3RT Contactors and SIRIUS 3RH2 Contactor Relays
Accessories
3
3RA28 function modules for mounting on 3RT2 contactors
and 3RH2 contactor relays
See pages 3/85 and 3/105
Simply by being plugged in place, the SIRIUS function modules
enable different functionalities required for the assembly of start-
ers to be realized in the feeder. The function modules and wiring
kits thus help to reduce the wiring work within the feeder practi-
cally to zero.
SIRIUS function modules for direct-on-line starting
The electronic timing relays which can be mounted onto the
contactor are available in these versions:
•
Sizes S00 and S0 for applications in the range from
24 to 240 V AC/DC (wide voltage range)
•
Sizes S2 and S3 for applications in either the range from
24 to 90 V AC/DC or 90 to 240 V AC/DC
Both the electrical and mechanical connection are made by sim-
ple snapping on and locking.
A protection circuit (varistor) is integrated in each module.
The electronic timing relay with semiconductor output uses two
contact legs to actuate the contactor underneath by means of a
semiconductor after the set time
t
has elapsed.
The switching state feedback is performed by a mechanical
switching state indicator (plunger). In addition, the auxiliary
switches in the contactors are freely accessible and can be used
for feedbacks to the control system or for signal lamps.
A sealable cover is available to protect against careless
adjustment of the set times.
The snap-on function modules for direct-on-line starting
are
used above all for realizing timing functions independently of the
control system.
With the OFF-delay variant of the timing relay it is possible for
example for the fan motor for cooling a main drive to be switched
off with a delay so that sufficient cooling after operation is guar-
anteed; the programmer of the control system does not need to
worry about such technical details of the plant.
The ON-delay timing relays enable for example the time-delayed
starting of several drives so that the summation starting current
does not rise too high, which could result in voltage failure.
The use of snap-on function modules for direct-on-line starting
results in the following advantages:
•
Reduction of control current wiring
•
Prevention of wiring errors
•
Reduction of testing costs
•
Implementation of timing functions independently of the
control system
•
Less space required in the control cabinet compared to a
separate timing relay
•
No additive protection circuit required (varistor integrated)
Assembly of reversing starters
We offer ready-made wiring kits for the assembly of reversing
starters. Use of these wiring kits offers further advantages;
see page 3/161
.
SIRIUS function modules for star-delta (wye-delta) starting
Both interlocking and timing functions are required for the
assembly of star-delta (wye-delta) starters. With the function
modules for star-delta (wye-delta) starting and the matching link
modules for the main circuit, these starters can be assembled
easily and with absolutely no errors.
The entire sequence in the control circuit is integrated in the
snap-on modules. This covers:
•
An adjustable star time
t
from 0.5 to 60 s
•
A non-adjustable dead interval of 50 ms
•
Electrical contacting of the contactors by means of coil
pick-off (contact legs)
•
Feedback of the switching state at the contactor using a
mechanical switch position indicator (plunger)
•
Electrical interlocking between the contactors
These modules do not require their own terminals and can there-
fore be used for contactors with both screw and spring-type
terminals in all the sizes S00 to S3. To start the star-delta (wye-
delta) starter, only the first of the three contactors (line contactor)
is actuated, like in the case of a direct-on-line starter. All other
functions then take place inside the individual modules.
This also offers advantages if the timing function was previously
implemented in a controller, as it again results in a significant
reduction in the number of PLC outputs, the programming work
and the wiring outlay.
The kits for the main circuit include the mechanical interlock, the
star jumper, the wiring modules at the top and at the bottom, and
the required connectors or connecting clips.
A protection circuit (varistor) is integrated in the basic module.
The function modules for star-delta (wye-delta) starting
are
mostly used where current-limiting measures for starting a drive
are required and a high level of availability is essential at the
same time. This technology has been used with success for
several decades and has the additional advantage of requiring
relatively little know-how. Through the use of function modules,
the assembly work with simple standard components is even
easier and absolutely error-free.
The use of function modules for star-delta (wye-delta) starting
results in the following advantages:
•
Operation solely through the line contactor A1/A2 – no further
control current wiring needed
•
Prevention of wiring errors
•
Reduction of testing costs
•
Integrated electrical interlocking saves costs and prevents
errors
•
Less space needed in the control cabinet compared to using
a separate timing relay
•
Adjustable starting in star mode from 0.5 to 60 s
•
Independent of the contactor's control supply voltage
(24 to 240 V AC/DC)
•
Varistor integrated – no additive protection circuit required
•
Mechanically coded assembly enables easy configuration
and reliable wiring
•
Fewer versions – one module kit for screw and spring-type
connection and for all the contactor sizes S00 to S3
•
Mechanical interlocking (with wiring kit for the main circuit)
© Siemens AG 2016