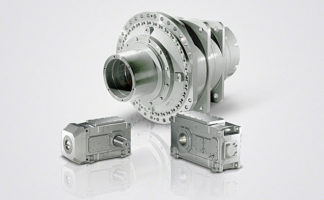
2/107
Siemens IC 10 · 2017
IO-Link
Introduction
IO-Link Specification
2
■
Overview
Principles of the IO-Link specification
According to the IO-Link specification, communication functions
as follows:
•
Transmission takes place via an unshielded three-wire cable
no more than 20 m long, of the kind normally used for standard
sensors.
•
Digital communication from 0 to 24 V on the so-called
C/Q cable
•
Most of the values transmitted are measured values from the
sensors
•
The sensors and actuators are described by the
IO Device Description (IODD)
•
As a matter of principle, one IO-Link device can be connected
to one IO-Link port of the master (point-to-point connection).
•
The transmission rates between IO-Link master and the
devices are as follows:
- via COM1: 4 800 Bd
- via COM2: 38 400 Bd
- via COM3: 230 400 Bd
•
The average cycle time is 2 ms for the reading/writing of
16 data bits at a transmission rate of 38 400 Bd.
IO-Link protocol
The IO-Link protocol supports both the Standard IO
mode (SIO) and the IO-Link communication mode (COM).
The structure of the protocol and its message frames depends on the
types of data to be transmitted.
Data types
The IO-Link specification makes a distinction between the
following data types:
Process data
The process data of the devices are transferred cyclically in a
data frame, with the process data width defined by the device.
Process data of 0 to 32 bytes are possible per device (input and
output in each case). The consistency width of the transmission
is not fixed and therefore depends on the master.
Value status
Each port has a value status (PortQualifier). The value status in-
dicates whether the process data are valid or invalid. The value
status can be transferred cyclically with the process data.
Device data
Device data can be parameters, identification data and diagnos-
tics information. Device data replacement is acyclic and in re-
sponse to an inquiry from the IO-Link master. Device data can be
written into the device (Write) and also read from the device
(Read).
Events
When an event occurs, the device sends a signal to the master
to report that an event is active. The master then reads out the
event. Events can be fault messages (e.g. short-circuit) and
warnings/maintenance data (e.g. contamination, overheating).
Fault messages are transferred from the device via the IO-Link
master to the controller or HMI. The IO-Link master can also
transfer events and states. Events include, for example, cable
break or communication breakdown.
Device parameters and events are sent independently of the
cyclic transmission of process data. The transmissions do not
affect or impair each other.
Data storage
As of Specification V1.1, a data storage concept has been
created for IO-Link. In this concept, the IO-Link device initiates
storage of its data on a higher-level parameter server. In the
event that a device is replaced, the parameter server can restore
the original parameterization. It is therefore possible to replace
the devices without re-parameterization.
The IO-Link master contains the parameter server. The parame-
ter server can also be implemented centrally in the PLC or in a
system server. In this case the data must be downloaded to the
control system by means of the function blocks provided.
IO-Link masters
The IO-Link master is the interface to higher-level control
systems. The IO-Link master presents itself to the fieldbus as a
normal fieldbus node, and is integrated into the appropriate net-
work configurator via the relevant device description (GSD file).
IO Device Description (IODD)
The IO Device Description (IODD) has been defined to provide
a full, transparent description of system characteristics as far as
the IO-Link device.
The IODD contains information on communication characteris-
tics, device parameters, identification, process and diagnostics
data, and is supplied by the manufacturer. The design of the
IODD is the same for all devices from all manufacturers, and is
always presented in the same way by the IODD Interpreter Tools.
This therefore ensures that the handling is the same for all
IO-Link devices, whatever the manufacturer.
New in IO-Link Specification V1.1
The IO-Link Specification is currently available in Version 1.1,
and standardized in accordance with IEC 61131-9.
Specification V1.1 offers the following new features compared
with the previous Specification V1.0:
•
Transmission of up to 32 bytes of process data in one cycle
•
Parameter server function
IO-Link master
Interface hardware:
Compatible with sensors according to IEC 60947-5-2 and actuators
Communication and switching possible alternately
IO-Link device
SIO
Standard IO
switching
operation
SIO / IO-Link
COM
Serial,
bidirectional
communication
IC01_00176
L+
C/Q
L–
4
1
2
3
© Siemens AG 2016