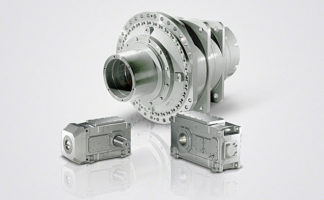
2/36
Siemens IC 10 · 2017
AS-Interface
Masters
Masters for SIMATIC ET 200
CM AS-i Master ST for SIMATIC ET 200SP
2
■
Overview
CM AS-i Master ST for SIMATIC ET 200SP
The CM AS-i Master ST communication module is designed for
use in the SIMATIC ET 200SP distributed I/O system and has the
following features:
•
Connection of up to 62 AS-Interface slaves
•
Supports all AS-Interface master functions according to the
AS-Interface Specification V3.0
•
User-friendly configuration with graphic display of the AS-i line
in TIA Portal V12 or higher, or via GSD in other systems
•
Supply via AS-Interface cable
•
Suitable for AS-i Power24V and for AS--Interface with 30 V
voltage
•
Integrated ground-fault monitoring for the AS-Interface cable
•
Through connection to AS-Interface, the number of digital
inputs and outputs available for the control system is greatly
increased (max. 496 DI/496 DQ on the AS-Interface per
CM AS-i Master ST).
•
Integrated analog value processing (all analog profiles)
ET 200SP distributed I/O system
The SIMATIC ET 200SP is a scalable and highly flexible
distributed I/O system for connecting the process signals to a
central control system via PROFIBUS or PROFINET.
Up to eight CM AS-i Master STs can be plugged into a SIMATIC
ET 200SP with the IM 155-6 PN standard interface module.
For more information,
see
"SIMATIC ET 200SP Distributed I/O system",
.
Design
The CM AS-i Master ST module has an ET 200SP module enclo-
sure with a width of 20 mm. A C0 type BaseUnit (BU) is required
for use in the ET 200SP.
The communication module has LED indicators for diagnostics,
operation, AS-i voltage and AS-i slave status and offers informa-
tive front-side module inscription for
•
Plain-text marking of the module type and function class
•
2D matrix code (Article No. and serial number)
•
Circuit diagram
•
Color coding of the CM module type: Light gray
•
Hardware and firmware version
•
Complete article number
Function
The CM AS-i Master ST
communication module supports all
specified functions of the AS-Interface Specification V3.0.
The input/output values of the digital AS-i slaves can be acti-
vated via the cyclic process image. The values of the analog
AS-i slaves are accessible via the cyclic process image
(firmware V1.1 or higher) or via data record transfer.
If required, master calls can be performed with the command
interface, e.g. read/write parameters, read/write configuration.
Changeover of the operating mode, automatic application of the
slave configuration and the re-addressing of a connected AS-i
slave can be implemented via the control panel of the
CM AS-i Master ST in STEP 7.
Expansions as from firmware version V1.1
For the implementation of modular machine concepts, the AS-i
Slaves can be activated or deactivated via the PLC program
(option handling). The configuration of AS-i slaves can be mod-
ified while being executed, thus enabling variable machine set-
ups and tool changing with integrated input/output modules
during ongoing operation. AS-i input/output modules can be
added to the system without deactivating the controller.
An existing AS-i installation can be read into the STEP 7 hard-
ware configuration and adapted and documented in the project.
Analog values are transmitted via the cyclic process image, the
length of which is adjustable and extendable up to 288 Bytes
(depending on the interface module (IM) used).
Diagnostic information is accessed via automatic alarm indica-
tions, via the process image or data record reading in the user
program or in the STEP 7 engineering system in a graphical
overview matrix. The transmission quality of the AS-i network
can also be read out. To avoid configuration errors, duplicate
addresses can be detected on the AS-i network.
The new functions are available with TIA Portal STEP 7 V13 SP1
or with STEP 7 V5.5 with HSP 2092 V3.0
1)
. Configuration is
possible with SIMATIC CPUs S7-300 up to S7-1500 and with a
SINUMERIK 840D sl or other controller.
In the network view, the AS-i slaves' online diagnostics status
can be displayed directly on the slaves (in the case of S7-1500
CPUs with updated TIA Portal STEP 7 V14 firmware or higher).
Notes on safety
In order to protect plants, systems, machines and networks
against cyber threats, it is necessary to implement – and contin-
uously maintain – a holistic, state-of-the-art industrial security
concept. Siemens products and solutions represent only one
component of such a concept.
For more information about the subject of Industrial Security,
see www.siemens.com/industrialsecurity
.
1)
For HSP 2092,
see
.
© Siemens AG 2016