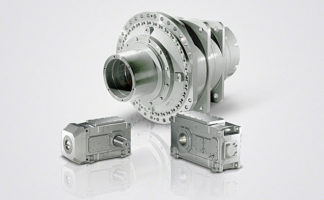
3/352
Siemens IK PI · 2015
■
Design
(continued)
PROFIBUS
PROFIBUS Components
PROFIBUS DP ASICs
3
SIM 1-2
The SIM 1-2 supplements the SPC 4-2 or DPC 31. Only a few
external components are required in addition to these ASICs to
be able to connect field devices to an intrinsically safe network
in accordance with PROFIBUS PA. In combination with the
SPC 4-2 or DPC 31, the functions of a PROFIBUS PA slave can
be processed from physical linking through to communication
control.
SIM 1-2 supports all send and receive functions (including
Jabber Control) as well as the high-resistance decoupling of
auxiliary power from the bus cable. It provides an adjustable,
stabilized supply voltage and also supports configuration of an
electrically isolating power supply with just a few passive
components.
The ASIC contains a special interface logic which provides
a low-overhead, minimum power interface for galvanic signal
separation as an alternative to the standard signal interface.
It can be connected to all Manchester encoders/decoders to the
IEC 61 158-2 standard at 31.25 kbit/s.
LSPM 2
LSPM 2 is a single-chip solution with 32 input/output bits. It
processes all bus communication autonomously. An additional
microprocessor and firmware are not required. The compact
MQFP casing with 80 pins makes it ideal for applications with
low space requirements.
FOCSI
This ASIC functions as an expansion to the existing PROFIBUS
ASICs. The FOCSI module (Fiber Optic Controller from Siemens)
ensures proper electrical conditioning and transfer of the re-
ceived/sent optical signal. To inject the signal into a fiber-optic
conductor, apart from FOCSI, the appropriate optical transmitter
and receiver will be required. FOCSI can be used with the
PROFIBUS DP ASICs described above.
Additional ordering data available on request
■
Technical specifications
LSPM 2
SPC 3
SPC 3LV
DPC 31
Protocol
PROFIBUS DP
PROFIBUS DP
PROFIBUS DP
PROFIBUS DP,
PROFIBUS PA
Application range
simple slave application
intelligent slave application
intelligent slave application
intelligent slave application
Transmission rate, max.
12 Mbit/s
12 Mbit/s
12 Mbit/s
12 Mbit/s
Bus access
in ASIC
in ASIC
in ASIC
in ASIC
Automatic determination of
transmission rate
yes
yes
yes
yes
Microprocessor required
no
yes
yes
integrated
Scope of firmware
not required
6 to 24 KB
6 to 24 KB
approx. 38 KB
Message buffer
-
1.5 KB
1.5 KB
6 KB
Power supply
5 V DC
5 V DC
3.3 V DC
3.3 V DC
Power loss, max.
0.35 W
0.5 W
<0.5 W
0.2 W
Permissible ambient temperature
-40 °C … +75 °C
-40 °C … +85 °C
-40 °C … +85 °C
-40 °C … +85 °C
Housing
MQFP, 80-pin
PQFP, 44-pin
PQFP, 44-pin
PQFP, 100-pin
Frame size
4 cm
2
2 cm
2
2 cm
2
4 cm
2
Delivery quantities (pcs.)
6/66/330/4 950
6/96/750/960/4 800
5/160/800/1 000/4 800
STEP B: 6/60/300/5 100
STEP C1: 6/66/660/4 620
SPC 4-2
ASPC 2
SIM 1-2
FOCSI
Protocol
PROFIBUS DP
PROFIBUS FMS
PROFIBUS PA
PROFIBUS DP
PROFIBUS FMS
PROFIBUS PA
PROFIBUS PA
-
Application range
Intelligent slave application
Master application
Medium Attachment
Medium Management Unit
Transmission rate, max.
12 Mbit/s
12 Mbit/s
31.25 kbit/s
12 Mbit/s
Bus access
in ASIC
in ASIC
-
-
Automatic determination of
transmission rate
yes
yes
-
-
Microprocessor required
yes
yes
-
-
Scope of firmware
3 … 30 KB
80 KB
not required
not required
Message buffer
3 KB
1 MB (external)
-
-
Voltage supply
5 V DC, 3.3 V
5 V DC
via bus
3.3 V DC
Power loss, max.
0.6 W at 5 V
0.01 W at 3.3 V
0.9 W
0.05 W
0.75 W
Permissible ambient temperature
-40 °C … +85 °C
-40 °C … +85 °C
-40 °C … +85 °C
-40 °C … +85 °C
Housing
TQFP, 44-pin
P-MQFP, 100-pin
MLPQ, 40-pin
TQFP, 44-pin
Frame size
2 cm
2
4 cm
2
36 mm
2
2 cm
2
Delivery quantities (pcs.)
5/160
6/66/660/4 620
30/60/1 000
40
© Siemens AG 2014