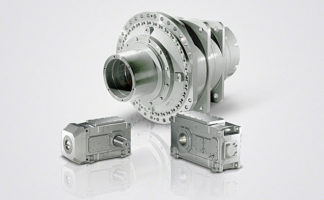
3/301
Siemens IK PI · 2015
PROFIBUS
SIRIUS 3RK3 Modular Safety System
General data
3
■
Overview
SIRIUS 3RK3 Modular Safety System
The 3RK3 Modular Safety System (MSS) is a freely parameter-
izable modular safety relay. Depending on the external circuit
version, safety-related applications up to Performance Level e
according to EN ISO 13849-1 or SIL 3 according to IEC 62061
can be realized.
The modular safety relay enables the interconnection of several
safety applications.
The comprehensive error and status diagnostics provides the
possibility of finding errors in the system and localizing signals
from sensors. Plant downtimes can be reduced as the result.
The MSS comprises the following system components:
•
Central units
•
Expansion modules
•
Interface modules
•
Diagnostics modules
•
Parameterization software
• Accessories
Central units
MSS Basic
The 3RK3 Basic central unit is used wherever more than three
safety functions need to be evaluated and the wiring parameter-
ization of safety relays would involve great cost and effort. It
reads in inputs, controls outputs, and communicates through an
interface module with higher-level control systems. An applica-
tion's entire safety program is processed in the central unit. The
3RK3 Basic central unit is the lowest expansion level and fully
functional on its own, without the optional expansion modules.
MSS Advanced
The 3RK3 Advanced central unit is the consistent expansion of
the Basic central unit with the functionality of an
AS-i safety monitor. In addition to having a larger volume of
project data and scope of functionality it can be
integrated in AS-Interface and therefore make use of the many
different possibilities offered by this bus system. The function
can be optionally activated in the central unit.
The service-proven insulation piercing method of AS-Interface
enables not only the distributed expansion of the project data
volume using safe AS-i outputs, safe AS-i sensors and other
MSS Advanced or safety monitors (F cross traffic) but also a
highly flexible adaptation of the application, e.g. very fast
connection of AS-i outputs such as LV HRC command devices,
position switches with and without interlock, or light curtains.
Safety-related disconnection using MSS or by distributed means
using safe AS-i outputs and the formation of switch-off groups
can be realized very easily. The same applies for any subse-
quent modifications. They are now easily possible by re-ad-
dressing, i.e. re-wiring is no longer necessary.
The AS-i bus is connected directly to the central unit.
MSS ASIsafe
The MSS ASIsafe basic and MSS ASIsafe extended central units
are a logical development of the AS-i safety monitors based on
the 3RK3 Modular Safety System.
Like MSS Advanced, MSS ASIsafe detects – in a comparable
way to the safety monitors – safe sensor technology on the AS-i
bus and switches actuators off in a safety-related manner via a
configurable safety logic. It stands out by virtue of its greater
project data volume, wider range of functions and the possibility
of increasing the integrated I/O project data volume by means of
expansion modules from the MSS system family. In this case the
range of functions, such as the number and type of the logic el-
ements that can be interconnected, is equivalent to that of MSS
Advanced.
Expansion modules
With the optional expansion modules, both safety-related and
standard, the system is flexibly adapted to the required safety
applications.
Interface modules
The DP interface module is used for transferring diagnostics
data and device status data to a higher-level PROFIBUS net-
work, e.g. for purposes of visualization using HMI. When using
the Basic central unit, 32-bit cyclic data can be exchanged with
the control system. If an Advanced/ASIsafe central unit is used,
the number is doubled to 64-bit cycle data. The acyclic calling
of diagnostics data is possible with all central units.
Diagnostics modules
Faults, e.g. cross-circuit, are indicated directly on the diagnos-
tics display. The fault is diagnosed directly in plain text by the
detailed alarm message. The device is fully functional upon
delivery. No programming is required.
Parameterization software
Using the MSS ES graphical parameterization tool it is very easy
to create the safety functions as well as their logical links on the
PC. It is therefore possible to define disconnection ranges, ON-
delays, OFF-delays and other dependencies for example.
MSS ES also offers comprehensive functions for diagnostics and
commissioning. Documentation of the MSS hardware configura-
tion and the parameterized logic is created automatically.
© Siemens AG 2014