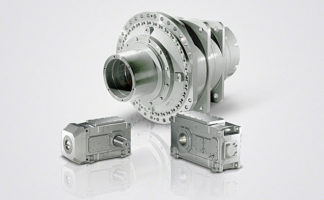
3/285
Siemens IK PI · 2015
PROFIBUS
SIMOCODE 3UF Motor Management and Control Devices
SIMOCODE pro
General data
3
■
Benefits
(continued)
Detailed operating, service and diagnostics data
SIMOCODE pro makes different operating, service and diagnos-
tics data available and helps to detect potential faults in time and
to prevent them by means of preventative measures. In the event
of a malfunction, a fault can be diagnosed, localized and recti-
fied very quickly – there are no or very short downtimes.
Operating data
•
Motor switching state derived from the current flow in the main
circuit
•
All phase currents
•
All phase voltages and phase-to-phase voltages
•
Active power, apparent power and power factor
•
Phase unbalance and phase sequence
•
Ground-fault current
•
Time to trip
•
Motor temperature
•
Remaining cooling time etc.
Service data
•
Motor operating hours
•
Motor stop times
•
Number of motor starts
•
Number of overload trips
•
Interval for compulsory testing of the enabling circuits
•
Energy consumed
•
Internal comments stored in the device etc.
Diagnostics data
•
Numerous detailed early warning and fault messages
•
Internal device fault logging with time stamp
•
Time stamping of freely selectable status, alarm or fault
messages etc.
Easy operation and diagnostics
Operator panel
The operator panel is used to control the motor feeder and can
replace all conventional pushbuttons and indicator lights to save
space. It makes SIMOCODE pro or the feeder directly operable
in the control cabinet. It features all the status LEDs available on
the basic unit and externalizes the system interface for simple
parameterization or diagnosis on a PC/PG.
Operator panel with display
As an alternative to the 3UF720 standard operator panel for
SIMOCODE pro V, there is also an operator panel with display:
the 3UF7 21 is thus able in addition to indicate measured values,
operating and diagnostics data or status information of the motor
feeder at the control cabinet. The pushbuttons of the operator
panel can be used to control the motor. Also, when SIMOCODE
pro V PROFINET is used it is possible to set parameters such as
rated motor current, limit values, etc. directly via the operator
panel with display.
Communications
SIMOCODE pro has either an integrated PROFIBUS DP inter-
face (SUB-D or terminal connection) or a PROFINET interface
(2 x RJ45).
Fail-safe disconnection through PROFIBUS or PROFINET with
the PROFIsafe profile is also possible in conjunction with a fail-
safe controller (F-CPU) and the DM-F PROFIsafe fail-safe digital
module.
SIMOCODE pro for PROFIBUS
SIMOCODE pro for PROFIBUS supports for example:
•
Cyclic services (DPV0) and acyclic services (DPV1)
•
Extensive diagnostics and hardware interrupts
•
Time stamp with high timing precision (SIMATIC S7) for
SIMOCODE pro V
•
DPV1 communication after the Y-Link
SIMOCODE pro for PROFINET
SIMOCODE pro for PROFINET supports for example:
•
Line and ring bus topology thanks to an integrated switch
•
Media redundancy via MRP protocol
•
Operating, service and diagnostics data via standard web
browser
•
OPC UA server for open communication with visualization and
control systems
•
NTP-synchronized time
•
Interval function and measured values for energy
management via PROFIenergy
•
Module exchange without PC memory module through
proximity detection
•
Extensive diagnostics and maintenance alarms
Notes on safety
For connection of an internal system to an external system,
suitable protective measures must be taken to ensure safe
operation of the plant (including IT security, e. g. network
segmentation).
More information see
www.siemens.com/industrialsecurity
.
SIMOCODE pro motor management and control devices with
communication function see page 3/288 onwards.
Accessories see page 3/293 onwards.
More information see Catalog IC 10, Chapter 14 "Parameteriza-
tion, Configuration and Visualization with SIRIUS", Industry Mall
or Interactive Catalog CA 01.
Autonomous operation
An essential feature of SIMOCODE pro is the autonomous exe-
cution of all protection and control functions, even when commu-
nication to the I&C system is interrupted. This means that even
in the event of bus system or automation system failure, full func-
tionality of the feeder is ensured or a specific behavior can be
parameterized in case of such a fault, e.g. targeted shutdown of
the feeder or execution of particular parameterized control
mechanisms (such as reversal of the direction of rotation).
© Siemens AG 2014