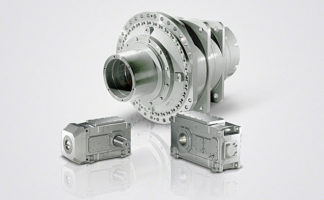
3/284
Siemens IK PI · 2015
PROFIBUS
SIMOCODE 3UF Motor Management and Control Devices
SIMOCODE pro
General data
3
■
Benefits
General customer benefits
•
Integrating the whole motor feeder into the process control by
means of PROFIBUS DP, PROFINET or OPC UA significantly
reduces the wiring outlay between the motor feeder and PLC.
•
Decentralization of the automated processes by means of
configurable control and monitoring functions in the feeder
saves resources in the automation system and ensures full
functionality and protection of the feeder even if the I&C or bus
system fails.
•
The acquisition and monitoring of operating, service and
diagnostics data in the feeder and process control system
increases plant availability as well as maintenance and
service-friendliness.
•
The high degree of modularity allows users to perfectly
implement their plant-specific requirements for each motor
feeder.
•
The SIMOCODE pro system offers functionally graded and
space-saving solutions for each customer application.
•
The replacement of the control circuit hardware with
integrated control functions decreases the number of
hardware components and wiring required and in this way
limits stock keeping costs and potential wiring errors.
•
The use of electronic full motor protection permits better utili-
zation of the motors and ensures long-term stability of the
tripping characteristic and reliable tripping even after years of
service.
Multifunctional, electronic full motor protection
for rated motor currents up to 820 A
SIMOCODE pro provides comprehensive protection of the motor
feeder by means of a combination of delayable, multi-level pro-
tection and monitoring functions:
•
Inverse-time delayed electronic overload protection
(CLASS 5 to 40)
•
Thermistor motor protection
•
Phase failure/unbalance protection
•
Stall protection
•
Monitoring of adjustable limit values for the motor current
•
Voltage and power monitoring
•
Monitoring of the power factor (motor idling/load shedding)
•
Ground-fault monitoring
•
Temperature monitoring, e.g. over PT100/PT1 000
•
Monitoring of operating hours, downtime and number of starts
etc.
Recording of measuring curves
SIMOCODE pro can record measuring curves and therefore is
able, for example, to present the progression of motor current
during motor start-up.
Flexible motor control implemented with integrated control
functions (instead of comprehensive hardware interlocks)
Many predefined motor control functions have already been
integrated into SIMOCODE pro, including all necessary logic
operations and interlocks:
•
Overload relays
•
Direct-on-line and reversing starters
•
Wye/delta starters (also with direction reversal)
•
Two speeds, motors with separate windings (pole-changing
starters); also with direction reversal
•
Two speeds, motors with separate Dahlander windings (also
with direction reversal)
•
Positioner actuation
•
Solenoid valve actuation
•
Control of a motor starter protector
•
Soft starter actuation (also with direction reversal)
These control functions are predefined in SIMOCODE pro and
can be freely assigned to the inputs and outputs of the device
(including PROFIBUS/PROFINET).
These predefined control functions can also be flexibly adapted
to each customized configuration of a motor feeder by means of
freely configurable logic modules (truth tables, counters, timers,
edge evaluation, etc.) and with the help of standard functions
(power failure monitoring, emergency start, external faults, etc.),
without additional auxiliary relays being necessary in the control
circuit.
SIMOCODE pro makes a lot of additional hardware and wiring in
the control circuit unnecessary which results in a high level of
standardization of the motor feeder in terms of its design and
circuit diagrams.
© Siemens AG 2014