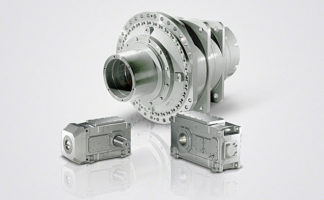
3/271
Siemens IK PI · 2015
PROFIBUS
Motor starters for use in the field, high degree of protection
M200D motor starters for PROFIBUS
3
■
Overview
(continued)
Parameterization and configuration
All motor protection functions, limit values and reactions can be
defined by parameterization.
The user has several user-friendly options for the parameteriza-
tion. In addition to parameterization directly from STEP 7, which
also permits automatic re-parameterization in case of device re-
placement, it is possible to use the user-friendly Motor Starter ES
start-up software. By connecting a programming device directly
to PROFIBUS/PROFINET and the Motor Starter ES start-up soft-
ware, the devices can also be conveniently programmed from a
central point through the bus. Also, parameters can be changed
during operation from the user program using the data record
mechanism so that the function of the motor starter is adapted to
the process when required. With the help of a PC and the Motor
Starter ES software it is also possible to perform the parameter-
ization through the local point-to-point interface on-site.
Functions can be flexibly assigned to the digital inputs and out-
puts, adapting them to all possible conveyor applications. All
digital inputs and outputs exist in the cyclic process image. All
limit values for monitoring functions and their reactions are pa-
rameterizable and therefore adaptable to the application. Con-
sistency with other products of the SIRIUS M200D motor starter
range and with the frequency converter and ET 200pro periph-
erals system is assured.
✓
Function available
--
Function not available
SIRIUS M200D
SIRIUS M200D
PROFIBUS
PROFINET
Device functions (firmware features)
Slave on the bus
Fieldbus
✓
PROFIBUS to M12
✓
PROFINET to M12
Adjustable number of stations
✓
1 ... 125
✓
1 ... 128 with CPU 315, CPU 317
1 ... 1 256 with CPU 319
Parameterization
DIP switches
✓
For address setting and terminating resistor
--
Motor Starter ES
✓
Through bus, optical interface
PROFIBUS/PROFINET data records
✓
From STEP 7 / HW Config
✓
Diagnostics
Acyclic through data records
✓
Diagnostic interrupt support
✓
Process image
Process image
✓
2Byte PII/ 2Byte PIQ
Data channels
Local optical interface (manual local)
✓
Through Motor Starter ES local interface
✓
Using Motor Starter ES through bus
✓
Data records (acyclic)
Parameterization
✓
Using DS 131 (DS = data record)
Diagnostics
✓
Device-specific DS 92
Measured values
✓
Measured values DS 94
Statistics
✓
Statistical data DS 95
Commands
✓
Using DS 93
Slave pointer
✓
Slave pointer DS 96
Logbook
✓
Using Motor Starter ES and data records: Device faults DS 72, tripping operations DS 73, events DS 75
Device identification
✓
Using DS 100
I&M data
✓
Using DS 231 ... 234
✓
Using data records 0xAFF0 ... 0xAFF3
Inputs
Number
✓
4
• Of which in the process image
✓
4
Input action
✓
Parameterizable: flexibly assignable action, see manual
Quick stop
✓
Parameterizable: latching, non-latching
© Siemens AG 2014