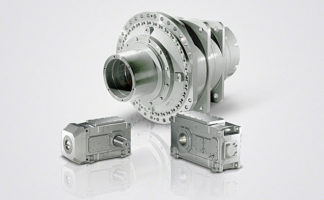
5/26
Siemens IK PI · 2015
IO-Link
SIRIUS 3RB24 solid-state overload relays for IO-Link
3RB24 for IO-Link, up to 630 A for High-Feature applications
5
■
Overview
SIRIUS 3RB24 evaluation module
The modular 3RB24 solid-state overload relay, which is powered
via IO-Link (with monostable auxiliary contacts) up to 630 A
(up to 820 A possible with a series transformer) have been
designed for inverse-time delayed protection of loads with
normal and heavy starting ("Function" see Manual
"SIRIUS 3RB24 Solid-State Overload Relay for IO-Link",
)
against excessive temperature rises due to overload, phase
unbalance or phase failure. It comprises an evaluation unit, a
current measuring module and a connecting cable.
The 3RB24 evaluation module also offers a motor starter
function: The contactors, which are connected via the auxiliary
contacts, can also be actuated for operation via IO-Link.
In this way, direct, reversing and star-delta starters up to 630 A
(or 830 A) can be connected to the controller wirelessly via the
IO-Link controller.
An overload, phase unbalance or phase failure result in an in-
crease of the motor current beyond the set rated motor current.
This current rise is detected by means of the current measuring
module (see page 5/30) and electronically evaluated by the
evaluation module which is connected to it. The evaluation elec-
tronics sends a signal to the auxiliary contacts. The auxiliary
contacts then switch off the load by means of a contactor.
The break time depends on the ratio between the tripping cur-
rent and current setting
I
e
and is stored in the form of a long-term
stable tripping characteristic (see "Characteristic Curves"
).
The "tripped" status is signaled by means of a continuously
illuminated red "
OVERLOAD
" LED and also reported as a group
fault via IO-Link.
The LED indicates imminent tripping of the relay due to overload,
phase unbalance or phase failure by flickering when the limit
current has been violated. This warning can also be reported to
the higher-level PLC via IO-Link at the 3RB24 overload relay.
In addition to the described inverse-time delayed protection of
loads against excessive temperature rises, the 3RB24 solid-
state overload relays also allow direct temperature monitoring of
the motor windings (full motor protection) by connection with
broken-wire interlock of a PTC sensor circuit. With this tempera-
ture-dependent protection, the loads can be protected against
overheating caused indirectly by reduced coolant flow, for ex-
ample, which cannot be detected by means of the current alone.
In the event of overtemperature, the devices switch off the
contactor, and thus the load, by means of the auxiliary contacts.
The "tripped" status is signaled by means of a continuously
illuminated "
THERMISTOR
" LED and also reported as a group fault
via IO-Link.
To protect the loads against incomplete ground faults due to
damage to the insulation, humidity, condensed water, etc.,
the 3RB24 solid-state overload relays offer the possibility of
internal ground-fault detection (for details, see Manual
"SIRIUS 3RB24 Solid-State Overload Relay for IO-Link",
,
not possible in conjunction with contactor assemblies for
wye-delta starting). In the event of a ground fault, the 3RB24
relays trip instantaneously.
The "tripped" status is signaled by means of a flashing red LED
"Ground Fault" and reported at the 3RB24 overload relay as a
group fault via IO-Link.
The reset after overload, phase unbalance, phase failure,
thermistor or ground-fault tripping is performed manually by key
on site, via IO-Link or by electrical remote RESET or automati-
cally after the cooling time (motor model) or for thermistor pro-
tection after sufficient cooling. Power cuts in devices due to
function monitors (broken wire or short-circuit on the thermistor)
can only be reset on-site ("Function" see Manual
"SIRIUS 3RB24 Solid-State Overload Relay for IO-Link",
).
`
_
^
]
\
[
Y
X
Y
Z
Plug-in point for operator panel:
enables connection of the 3RA6935-0A operator panel.
Motor current and trip class setting:
Setting the device to the motor current and to the required trip
class dependent on the start-up conditions is easy with the two
rotary switches.
Connecting terminals (removable terminal block):
The generously sized terminals permit connection of two
conductors with different cross-sections for the auxiliary, control
and sensor circuits. Connection is possible with screw connection
and alternatively with spring-type connection.
Test/RESET button:
Enables testing of all important device components and functions,
plus resetting of the device after a trip when manual RESET is
selected.
Selector switch for manual/automatic RESET:
With this switch you can choose between manual and automatic
RESET.
Red LED "OVERLOAD":
A continuous red light signals an active overload trip; a flickering
led light signals an imminent trip (overload warning).
Red LED "THERMISTOR":
A continuous red light signals an active thermistor trip.
Red LED "GND FAULT":
A continuous red light signals an active ground-fault trip.
Green LED "DEVICE/IO-Link:
A continuous green light signals that the device is working
correctly, a green flickering light signals the communication
through IO-Link.
X
Y
Z
`
_
^
]
\
[
NSB0_02180b
© Siemens AG 2014