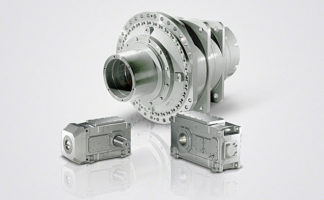
2/603
Siemens IK PI · 2015
PROFINET/Industrial Ethernet
Communication for PC-based systems
CP 1613 A2
2
■
Function
User interfaces
OPC interface
The OPC server included in the respective software package
can be used as the standard programming interface for the
protocols S7 communication and open communication, in order
to connect automation technology applications to OPC-compat-
ible Windows applications (Office, HMI systems, etc.)
Programming interface through C library
The programming interfaces for the S7 communication, PG/OP
communication, and open communication protocols for existing
applications are implemented as Dynamic Link Library (DLL)
interfaces.
You can find the released compilers in the Readme file
of the SIMATIC NET CD products at
.
Software for PG/OP communication
This software makes it possible to program the S7 controllers via
Industrial Ethernet in conjunction with the STEP 7 engineering
software.
It is included in all CP 1613 A2 software packages.
Software for S7 communication
(HARDNET-IE S7 or S7-REDCONNECT)
The S7 interface allows PG/PC applications (e.g. WinCC) and
user programs to access the SIMATIC S7 system components.
This provides easy, flexible access to the data of the SIMATIC S7
controller.
S7 communication offers:
Administrative services
•
Connection management
•
Mini database
• Trace
Data transfer services
•
Read/write variables
• BSEND/BRECEIVE
H-communication
For redundant S7 communication with a high availability
S7-400H system, the CP 1613/CP 1623/CP 1628 can be used in
connection with the S7-REDCONNECT software.
Software for open communication (SEND/RECEIVE)
This interface is used for communication between
•
PG/PC and SIMATIC S5
•
PG/PC and SIMATIC S7
•
PG/PC and PG/PC
Open communication (SEND/RECEIVE) offers the following
services:
•
Management services
•
Connection establishment services
•
Data transfer services
These functionalities are a component part of the
HARDNET-IE S7 software product.
Mode of operation
Protocols up to Level 4 (Transport) are processed autonomously
on the module.
16 MB of memory is available for this to support a large quanti-
tative framework and reliable communication.
Data is exchanged between the module and the host in master
mode. This means that the CP 1613 A2 accesses the physical
RAM of the host.
A Windows driver is responsible for transferring data between
the host system and the CP 1613 A2. The transmission rate to
Industrial Ethernet is detected and automatically switched over
(autosensing).
The IT functionality is provided in combination with the Windows
software of the PC.
Diagnostics
Via SNMP all MIB-2 objects can be read out. This enables the
current status of the Ethernet interfaces to be retrieved.
Configuration
•
The S7 communication and open communication protocols
are configured in STEP 7 or NCM PC.
•
A configuration tool is included in the scope of delivery of the
CP 1613 A2 software packages.
© Siemens AG 2014