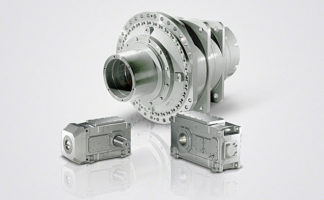
2/18
Siemens MD 31.1 · 2016
Configuring guide
Configuring SIP planetary geared motors and SIP planetary gear units
Selection example for SIP planetary gear unit
2
■
Configuring
(continued)
Application example
Customer data for design example:
•
Bevel planetary gear unit
•
Hollow shaft with shrink disk
•
Variant 1
:
Selected motor
P
n
= 4 kW IEC 112M Siemens LE16….
•
Variant 2
:
Operational torque
T
2
= 38200 Nm is known
•
Input speed of customer system 1.0 rpm
•
Maximum 4 starts per hour, duty 24 h/day
•
Smooth operation
Selection sequence
Notes, references
Planetary gear unit
Type of drive concept
Variant 1:
• Motor nominal power
P
N
• Speed of driven machine
n
2
Primary input variables
Start of example calculation
process for a planetary gear unit
with motor power.
Calculate the required motor power
•
T
2
operational torque
•
n
2
speed of driven machine
(customer data)
•
P
N
motor nominal power
assigned by selection of motor
In the first step, the operational
torque is calculated on the basis of
the motor power. Please pay atten-
tion to the units of measurement!
Motor power in [kW] and speed in
[rpm]. The result is measured in
unit [Nm].
Variant 2:
• Operational torque
T
2
• Speed of driven machine
n
2
Primary input variables
Start of example calculation
process for a planetary gear unit
with operational torque. Starting
the process using the operational
torque supplied by the customer
allows precise selection.
Calculate the required nominal torque of the gear unit
•
T
2req
required nominal torque
of gear unit
•
T
2
operational torque
•
f
B
service factor:
pages 2/10 to 2/11
In the second step, the operational
torque must be multiplied by the
service factor in order to determine
the required nominal torque.
T
2
=
= 38200 Nm
=
P
N
× 9550
n
2
4 kW
× 9550
1 rpm
T
2req
=
T
2
×
f
B
=
38200 Nm × 1.5 = 57300 Nm
© Siemens AG 2016