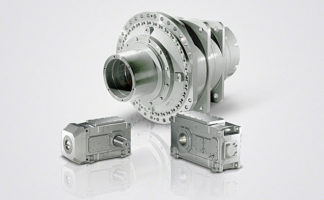
2/14
Siemens MD 31.1 · 2016
Configuring guide
Configuring SIP planetary geared motors and SIP planetary gear units
Selection example for SIP planetary geared motor
2
■
Configuring
(continued)
Application example
Customer data for design example:
•
Bevel planetary gear unit
•
Hollow shaft with shrink disk
•
Mounted with torque arm
•
Variant 1: Operational torque
T
2
= 33500 Nm is known
•
Variant 2: Required power
P
2
= 3.5 kW is known
•
Input speed of customer system 1.0 rpm
•
Maximum 4 starts per hour, duty 24 h/day
•
Smooth operation
Selection sequence
Notes, references
Planetary geared motor
Type of drive concept
Variant 1:
• Operational torque
T
2
• Speed of driven machine
n
2
Primary input variables
Calculate the required motor power
•
P
2
required motor power must be calculated
•
T
2
operational torque (customer data)
•
n
2
speed of driven machine (customer data)
•
P
N
motor nominal power assigned by selection of IEC standard
motor
Variant 2:
• Required power
P
2
• Speed of driven machine
n
2
Primary input variables
Select the motor nominal power
• Coaxial shaft arrangement:
Chapter 3
• Right-angle shaft arrangement:
Chapter 4
P
N
is printed in the first column
Catalog excerpt from page 4/18
Select
n
2
and
f
B
• Coaxial shaft arrangement:
Chapter 3
• Right-angle shaft arrangement:
Chapter 4
n
2
and
f
B
are printed in columns 2 and 3
For calculation of
f
B
see pages 2/10 and 2/11
Catalog excerpt from page 4/18
P
2
=
P
2
= 3.5 kW ≤
P
N
= 4 kW
= 3.5 kW
=
T
2
×
n
2
9550
33500 Nm
× rpm
9550
P
2
≤
P
N
© Siemens AG 2016