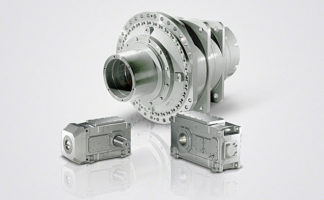
2/10
Siemens MD 31.1 · 2016
Configuring guide
Configuring SIP planetary geared motors and SIP planetary gear units
Key to symbols
2
■
Configuring
(continued)
Thermal factor f
4
The thermal factor corrects the thermal performance capability
of the gear unit, i.e. its
thermal capacity
, under conditions that
deviate from normal values. The thermal factor is influenced by
two parameters, i.e. the
ambient temperature
and the relative
on-load factor
.
Standard values:
20 °C
t
A
and
E
D
100 %
30 °C
t
A
and
E
D
60 %
For other values, please use the information in the table on
page 2/12.
Altitude factor f
6
The altitude at which the gear unit is installed influences the
thermal performance capability of the gear unit, i.e. its
thermal
capacity
. The higher the installation altitude of the drive, the
lower the volume of heat that can be dissipated via the housing
surface (convection).
Service factor f
B
The service factor is a mechanical engineering parameter that
combines the load types and specific features associated with a
particular application, and with the motor and gear unit for
design purposes. The service factor therefore has a decisive
influence on the selection of an optimum gear unit.
A distinction is made between the following two key
determinants:
•
Prime mover
•
Driven machine
The service factor is calculated as follows:
Provided that the prime mover has a uniform torque curve
(electric or hydraulic motors, turbines), this influence can be
ignored (
see factor for prime mover
f
2
)
.
For the majority of customer applications, this means that the
service factor can be set to the same value as the
factor for the
driven machine
f
1
.
If the service factor is too low, there is a risk that the gear unit will
be unintentionally underdimensioned. This would result in higher
wear and thus potentially premature failure of the gear unit. An
excessively high service factor would by contrast result in an
overdimensioned gear unit, possibly resulting in a poorer com-
petitive position due to selection of an oversized gear unit.
The service factor can be referred to the motor power output
P
N
or to the power rating of the driven machine
P
2
.
P
2
is often used in the calculation in the case of large motor
reserves.
With this method of calculation, however, it must also
be ensured that the maximum torque
P
max
of the gear unit is
never exceeded.
In order to select the most optimum service factor possible, we
recommend the following procedure:
Specification of the
factor of the driven machine
f
1
by the
customer – the system manufacturer generally has the greatest
expertise and knowledge with respect to load cycles and load
characteristics of the relevant application.
If this information is not available, then the following procedure
is recommended:
If there is insufficient information available about the load cycle
and or the on-load factor, it is possible to select a
factor for the
driven machine
f
1
on the basis of the following overview.
ƒ
B
= ƒ
1
× ƒ
2
© Siemens AG 2016