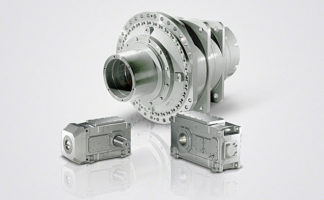
2/9
Siemens MD 31.1 · 2016
Configuring guide
Configuring SIP planetary geared motors and SIP planetary gear units
Key to symbols
2
■
Configuring
(continued)
Ambient temperature t
A
The temperature of the environment in which a drive operates
has a huge influence on the thermal budget of the gear unit and
therefore directly affects its endurance and service life.
The higher the ambient temperature, the higher the operating
temperature of the gear unit. The higher the operating tempera-
ture of the gear unit, the higher the stress on the lubricant/oil. The
specified product characteristics are in turn largely attributable
to the lubricant/oil used.
Likewise, very low ambient temperatures have a direct influence
on the gear unit design. Extremely low temperatures can alter
the mechanical properties of the materials used in the manufac-
ture of individual components. Depending on the type of temper-
ature-related stress, counter-measures (such as startup temper-
ature limiting or use of an oil heating system) must be taken.
The manufacturer must always be consulted if the ambient
temperature for an application is lower than -40 °C or higher than
50 °C.
Required motor power P
2
(power rating of driven machine)
The term "required motor power" refers to the motor power output
that is needed in order to create a suitable drive system for the
customer's process. The required motor power depends on the
speed at which the driven machine is required to operate. It is
also referred to as the "power rating of the driven machine". The
required motor power might also include correction factors
depending on the
duty type
and
ambient conditions
. These
correction factors might be:
•
k
ED
– factor for increased power
•
Z
perm
– permissible switching frequency
•
k
HT
– factor for coolant temperature and installation altitude
For further information about factors, refer to Catalog MD 50.1,
Chapter 2, Configuring a three-phase motor, or refer to the
relevant motor catalog.
Motor nominal power P
N
The motor nominal power is the nominal output power of the
prime mover.
Thermal capacity P
G
The term "thermal capacity" expresses the power that can be
continuously transmitted by the gear unit at a specific ambient
temperature. If the input power to the gear unit exceeds the
thermal capacity of the gear unit over a prolonged period of
time, its service life will be reduced and/or gear components will
be damaged. The thermal capacity depends on the following
factors:
•
Size of the gear unit
– the larger the selected gear unit, the
higher its thermal capacity.
•
Ambient temperature
– the higher the ambient temperature,
the lower the thermal capacity of the gear unit (because less
heat can be dissipated to the environment).
•
Installation altitude
– the higher the altitude at which the gear
unit operates, the less heat can be absorbed by the environ-
ment (see
altitude factor
).
•
Wind speed
– the greater the wind speed, the greater the
volume of heat that can be dissipated to the environment
(air cooling principle).
•
Speed of prime mover
n
1
and
gear unit output speed
n
2
–
the higher the speed of a gear stage, the higher the
associated heat losses and thus the higher the temperature
rise in the gear unit.
Note
: It may be possible to reduce heat losses and thus also the
temperature rise in the gear unit by selecting a suitable oil grade
and oil viscosity. Please contact the manufacturer for further
information.
Maximum output power P
max
The term "maximum output power" refers to the maximum
permissible short-time power output of the gear unit. The maxi-
mum output power is dependent on various parameters and
must be recalculated for each gear unit design. The gear unit
power output must never exceed this maximum value.
On-load factor E
D
The term "on-load factor" refers to continuous operation of an
item of equipment (drive system), expressed as a percentage,
over a given time period or, when no specific time period is
stated, over a period of ten minutes.
Factor for driven machine f
1
Three criteria are generally taken into account in the design of
gear units:
•
Design features of the gear unit
(type of machine elements, materials used, etc.)
•
Design features of the driven machine
•
Specific features of the type of application (load cycle)
In most cases, insufficiently accurate data about customer-
specific features such as design details or load cycle are avail-
able at the time a gear unit is configured. These unknown vari-
ables are expressed as a percentage in the factor for the driven
machine.
Factor for prime mover f
2
The factor for the prime mover takes into account the character-
istics of the driving motor and its influence on the gear unit.
Owing to their irregular torque curve, piston stroke engines have
the most serious affect on gear units. Since this type of prime
mover is rarely or only sporadically deployed in industry, it is safe
to assume a prime mover factor of 1.0 for most applications.
Peak torque factor f
3
The peak torque factor takes into account two basic load
scenarios, i.e.
pulsating load and alternating load
.
The correction factor can be understood as the product of
these two load types and it corrects the performance
capability of the gear unit accordingly.
The following generalized statement is true:
The more frequently a peak load occurs, the lower the
performance capability of the gear unit.
If this peak load occurs in conjunction with a reversal in the
direction of load, the loss of performance of the gear unit is even
greater.
Elements of a load cycle that influence the design of a gear unit:
•
Number of load peaks per hour
•
Reversal in direction of load
Period
100 %
10 min operation
80 %
8 min operation, 2 min interruption
60 %
6 min operation, 4 min interruption
…
…
© Siemens AG 2016