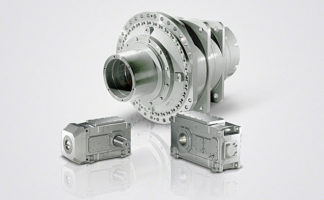
2/8
Siemens MD 31.1 · 2016
Configuring guide
Configuring SIP planetary geared motors and SIP planetary gear units
Key to symbols
2
■
Configuring
(continued)
Operational torque T
2
The term "operational torque" refers to the torque that is required
to create a suitable drive system for the customer's process. The
operational torque does not include any supplementary factors
that may be relevant for the selection of an appropriate drive
unit.
Depending on the individual application, the operational torque
curve can be almost linear, or variable/cyclical. For an applica-
tion with a variable torque curve, it is possible to calculate an
equivalent torque, i.e. to convert the variable torque into a quasi
linear curve.
See variable output/torque.
Variable output/torque
For driven machines with constant speeds and variable power
ratings the gear unit can be designed according to the
equivalent power rating. For this a working cycle where phases
I, II ... n require power
P
I
,
P
II
...
P
n
and the respective power
ratings operate for time fractions
X
I
,
X
II
...
X
n
is taken as a basis.
The equivalent power rating can be calculated from these
specifications with the following formula:
The size of the gear unit can then be determined analogously to
points 1.1 ... 1.5 and 3.
The following applies:
Then, when
P
2N
has been determined, the power and time
fractions must be checked by applying the following
requirements:
•
The individual power fractions
P
I
,
P
II
…
P
n
must be greater
than 0.4 x
P
2N
.
•
The individual power fractions
P
I
,
P
II
...
P
n
must not exceed
1.4 x
P
2N
.
•
If power fractions
P
I
,
P
II
...
P
n
are greater than
P
2N
, the sum of
time fractions
X
I
,
X
II
…
X
n
must not exceed 10%.
If any one of the three requirements is not met,
P
2eq
must be
recalculated.
It must be borne in mind that a brief peak power rating not
included in the calculation of
P
2eq
must not be greater than
P
max
= 1.5 x
P
2N
.
In applications where the torque is variable but the speed
constant, the gear unit can be designed on the basis of the
so called equivalent torque.
A gear unit design which is finite-life fatigue-resistant can be
sufficient for certain applications, This includes, for example,
sporadic operation (e.g. lockgate drives).
Example: Service classification
In the case of a service classification, you will need to contact us.
Required nominal torque T
2req
The term "required nominal torque" refers to the torque that is
required to create a suitable drive system for the customer's
process. This includes
the selected correction factors such as
the
factor for driven machine
f
1
and the factor for prime
mover
f
2
.
Gear unit nominal torque T
2N
The term "gear unit nominal torque" refers to the torque that may
be applied continuously to the low speed shaft of the relevant
gear unit.
Maximum gear unit torque T
2max
The term "maximum torque" refers to the highest permissible
torque that may be briefly applied to the relevant gear unit.
It is calculated from the nominal torque
T
2N
and the peak torque
factor
f
3
of the relevant application.
The maximum torque must not be exceeded by torques
produced during peak operation, startup, braking, etc.
Prime mover speed n
1
The term "prime mover speed" refers to the speed produced by
the prime mover (electric, hydraulic or air motor, or combustion
engine). The speed curve can be linear or cyclical.
Gear unit output speed n
2
The term "gear unit output speed" refers to the speed of the low
speed gear unit shaft as a function of the
prime mover speed
and the
ratio
of the gear unit. The gear unit output speed is not
always the same as the setpoint quantity
speed of driven
machine
. A gear unit with an output speed closest to the
setpoint quantity must be selected. If the divergence between
the two speeds is still unacceptable, the deviation can be
minimized further or completely eliminated by varying the
speed
of the prime mover
(e.g. by installing a frequency converter).
Total transmission ratio i
tot
The total transmission ratio is the ratio between
n
1
and
n
2
.
n
II
I
100
X
I
100
X
II
P
2eq
=
100
X
n
+ P
6.6
+ ... P
6.6
6.6
P
6.6
P
2N
≥
P
2eq
f
1
f
2
P
2eq
G_MD30_EN_00043
X
l
=15%
X
=100%
X
lV
=15%
X
lI
=30%
X
lII
=40%
I
II
III
IV
P
ll
P
l
P
X
P
lll
P
lV
T
2max
=
T
2N
f
3
i
tot
=
n
1
n
2
© Siemens AG 2016