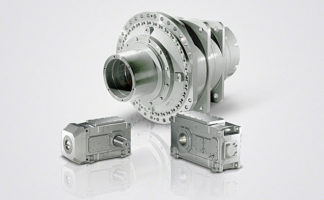
2/6
Siemens MD 31.1 · 2016
Configuring guide
Configuring SIP planetary geared motors and SIP planetary gear units
Configuring sequence – selection according to torque
2
■
Configuring
(continued)
Selection according to operational torque T
2
– planetary gear unit
(for selection according to power output,
see page 2/4
)
Selection sequence
Notes, references
• Operational torque
T
2
• Speed of driven machine
n
2
Primary input variables
Planetary gear unit
(Geared motor: see page 2/4)
Type of drive concept
Specification of service factor
f
B
–
selection according to application:
or defined according to customer requirements
•
f
B
service factor – definition
page 2/10
•
f
1
factor for driven machine – definition
page 2/9
•
f
2
factor for prime mover – definition
page 2/9
•
f
1
values:
page 2/11
•
f
2
values:
page 2/12
Calculate the required gear unit nominal torque:
•
T
2req
required gear unit nominal torque – definition
page 2/8
•
T
2
see first step
•
f
B
service factor,
see previous step
Select the gear unit size
•
T
2N
gear unit nominal torque – definition
page 2/8
•
T
2N
values:
page 2/12
Selection of shaft arrangement of gear unit
Coaxial or at right angles
Select a gear unit with
i
tot
or
n
2
•
i
tot
total transmission ratio – definition
page 2/8
• Coaxial shaft arrangement:
Chapter 5
• Right-angle shaft arrangement:
Chapter 6
Select an adapter type (motor flange)
The adapter selection depends on the type of motor selected.
Adapter types:
page 5/2 or page 6/2
Thermal capacity check
O4/O5:
The thermal limits of application are determined by the input drive
assembly (SIMOGEAR geared motor).
O2:
• As a general rule, the solutions offered in
Chapters 5 and 6
are safe
and reliable in operation up to a motor speed of 1500 rpm and an
ambient temperature of 40 °C.
•
See Catalog MD 50.1
for configuring guide
• An arithmetic analysis is performed for O2 variants.
•
P
G
thermal capacity – definition
page 2/9
•
P
G
values:
from page 2/13 onwards
•
f
4
thermal factor – definition
page 2/10
•
f
6
altitude factor – definition
page 2/10
•
f
4
and
f
6
values:
page 2/12
Calculation of the maximum permissible torque
The maximum permissible torque must not be exceeded by torques
produced during peak operation, startup or braking.
•
T
max
maximum torque – definition
page 2/8
•
T
2N
gear unit nominal torque – definition
page 2/8
•
T
2N
values:
page 2/12
•
f
3
peak torque factor – definition
page 2/9
•
f
3
values:
page 2/12
Read article number from table
• Coaxial shaft arrangement:
from page 3/3 onwards
• Right-angle shaft arrangement:
from page 4/3 onwards
Complete the article number
1. Output shaft geometry
2. Type of installation
3. Selection of mounting position
• Output shaft geometry:
-
Selection guide:
page 2/7
-
Dimensions of coaxial version:
page 3/96
-
Dimensions of right-angled version:
page 4/81
• Installation:
see pages 10/2 to 10/5
• Mounting position:
-
Overview,
see pages 1/4 and 1/5
-
Ordering data,
see pages 10/7 and 10/8
Selection of other options and properties
See Chapter 9
ƒ
B
= ƒ
1
× ƒ
2
T
2req
=
T
2
×
f
B
T
2N
≥
T
req
P
2
≤
P
G
×
f
4
×
f
6
T
max
=
T
2N
ƒ
3
© Siemens AG 2016