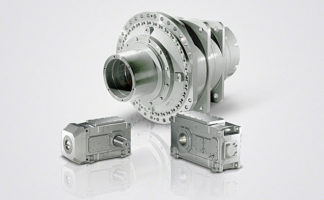
1/7
Siemens MD 31.1 · 2016
Introduction
Technical information
1
■
Overview
(continued)
Direction of rotation
The specified direction of rotation refers to the low speed shaft
(LSS) when viewing the shaft end face.
Bearings
The bearings of the gear wheels and shafts are always roller
bearings that are appropriately dimensioned in terms of stress
resistance and service life.
The bearing service life is calculated in accordance with
ISO 281 and the manufacturer's data.
Lubrication/selection of oil
FLENDER SIP planetary gear units/geared motors are dip-lubri-
cated. With this lubrication method, all parts to be lubricated are
immersed in oil or are adequately splash lubricated.
Only oils supplied by manufacturers that are approved by
Siemens AG may be used. The oil manufacturer or supplier is
responsible for the quality of the product.
For the selection of oil grade and viscosity, the limits of applica-
tion given in the following table must be taken into consideration.
Please also refer to the Operating Instructions 7300 for details of
the recommended lubricants.
A minimum operating viscosity of 25 cSt must be ensured.
Furthermore, the oil sump temperature must not be lower than
the pour point of the selected oil grade, and should be at least
6 K higher than the pour point temperature.
In the case of ambient temperatures outside the permissible
range, you will need to contact us.
The planetary gear units/geared motors are filled with oil as
standard before they are shipped. Shipment without oil can be
selected as an option.
The oil quantities depend on the oil level inspection devices.
Relevant information can be found in Operating Instructions
9300. Siemens reserves the right to make technical changes
in the context of further technical development.
It must also be noted that 4 and 5-stage (O4…, O5…) planetary
gear units/geared motors have 2 separate oil chambers
(oil chamber for planetary stages, oil chamber for input drive
assembly) that need to be filled separately
(
see Operating Instructions BA 9300 and BA 2030
).
Further information about selecting oil can be found in chapter 9.
Oil-level-specific symbols in the dimensional drawings:
Permissible additional forces
The maximum permissible radial force (dynamic or static) ap-
plied to the low speed shaft (LSS) is specified. This is calculated
on the basis of the nominal bearing service life L
10h
(according
to ISO 281). This applies to shaft type K (hollow shaft with spline)
with a force application point at the center of the spline.
The values are specified in the selection tables.
Higher radial forces, other force-application points or different
shaft types are available on request.
Please contact the manufacturer for information about the
maximum permissible radial forces at the high speed shaft
(HSS) on 2-stage planetary gear units (O2…); the information
in the SIMOGEAR catalog (MD 50.11) relating to 4 and 5-stage
gear units (O4..., O5) must be taken into account.
Information about axial force application must be requested.
Gear teeth
The sun pinion and planet gears have straight teeth, are case
hardened, and ground. Internal gears are highly tempered and
manufactured by hobbing. Helical stages comprise spur gears
with helical teeth, and bevel gear stages are constructed of
bevel gears with spiral teeth.
Number of teeth, ratio
The specified number of gear teeth applies to the complete
drive.
Housing
The housing parts are constructed of casting materials
customary in the industry. They are also primed and painted.
Viscosity ISO-VG at
40 °C in mm
2
/s (cSt)
Minimum temperature limit in °C for
dip lubrication
Mineral oil
PAO oil
1)2)
220
-10
-30
320
-10
-30
460
-6
-25
Symbol
Explanation
Oil level screw
Breather
Oil filler
Oil drain
Oil dipstick
1)
PAO oil: Polyalphaolefin-based synthetic oil
2)
PAO-T oil: Synthetic polyalphaolefin-based low-temperature oil
© Siemens AG 2016