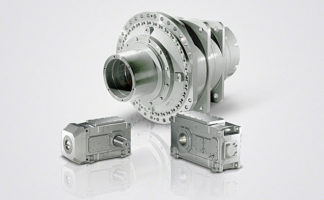
1/6
Siemens MD 31.1 · 2016
Introduction
Technical information
1
■
Overview
Planetary gear unit
Planetary gear unit which is connected to the motor by means
of a coupling element
. Various adapter options are available for
connecting the motor.
See Adapters on page 5/2 or 6/2.
Planetary geared motor
Planetary gear unit with an integral motor connection
. In this me-
chatronic system, the motor shaft also functions as the first input
element of the gear unit. This arrangement reduces the maxi-
mum overall dimensions of the unit.
See planetary geared motor
in chapter 3 or 4.
Options
The term "Options" is used to describe additional properties and
features of the drive solution that are not directly related to the
torque and speed conversion capabilities of the gear unit. Exam-
ples of options are: Different types of low speed shaft, seal vari-
ants, sensors, paint systems, torque arm, etc.
Features such as size, gear ratio or design are not options be-
cause these all have a significant influence on the gear unit itself.
Article number
All features that uniquely define a product are encoded in the
article number. The article number is a machine-
readable product code (MLFB).
Motors
Any of the SIMOGEAR motors listed in Catalog MD 50.1 can be
selected as a planetary geared motor. Thanks to the very wide
range of transmission ratios of the gear units, 4-pole motors can
be used for a broad range of applications. In addition to the
good availability worldwide, 4-pole motors generally offer the
optimum solution regarding price, length, noise and service life.
Furthermore, motors with other pole numbers can also be
mounted. As a consequence, the following special combina-
tions can be implemented:
•
Higher output speeds (2-pole motors)
•
Low output speeds (6-pole motors or possibly
8-pole motors)
•
Lower noise solutions (6-pole motors)
Motors can be supplied by a frequency converter to create a
variable-speed drive.
For further information, please refer to chapter "Motors" or to the
SIMOGEAR Catalog MD 50.1.
High speed shaft (HSS)
On 2-stage planetary gear units (O2), the high speed shaft
(HSS) is designed as a free shaft end (A) with a parallel key in
accordance with DIN 6885-1 and is suitable, for example, for the
attachment of couplings.
A variety of adapters that allow standard motors of various kinds
to be connected to the gear unit are available for 4 and 5-stage
planetary gear units.
For further information about this and the
types of high speed shaft (HSS) available, please refer to chap-
ter "Planetary gear units" and the SIMOGEAR Catalog MD 50.11.
Low speed shaft (LSS)
Various types of low speed shaft (LSS) (as listed in the summary
of basic types in this chapter) are available for planetary gear
units and planetary geared motors.
In addition, a flange for the connection to the driven machine is
fitted at the low speed shaft (LSS) end. A torque arm must be
provided for shaft-mounted gear units/geared motors (chapter
"Options for installation and attachment parts"). The unit can also
be installed by means of a gear housing base (chapter "Options
for installation and attachment parts") that is bolted to the flange
at the low speed shaft (LSS) end.
During installation of the gear unit, it is important to comply with
the manufacturer's specifications regarding tightening torques,
connection of the torque arm to the foundation and attachment
points for lifting/holding the gear unit (see Operating Instructions
9300 and order-specific gear unit documentation). Failure to
install the unit in accordance with specifications can affect its
ability to function correctly.
Shafts
The load-bearing capacity of the shafts of planetary gear
units/geared motors is calculated in accordance with DIN 743.
Further information about the design and dimensioning of
the shaft ends of low and high speed shafts can be found in
sections "Input end" and "Output end". Information about the
centering at the shaft ends can be found in chapter
"Connection dimensions" and in Catalog MD 50.11.
Shaft misalignment
Shaft misalignment is the result of displacement during assem-
bly and operation and, where machines constructed with two
radial bearings each are rigidly coupled, will cause high loads
being placed on the bearings. Elastic deformation of base
frame, foundation and machine housing will lead to shaft mis-
alignment which cannot be prevented, even by precise align-
ment. Furthermore, because individual components of the drive
train heat up differently during operation, heat expansion of the
machine housings causes shaft misalignment.
Poorly aligned drives are often the cause of seal or roller bearing
failure. Alignment should be carried out carefully by specialist
personnel and in accordance with the Siemens operating in-
structions.
Depending on the direction of the effective shaft misalignment,
a distinction is made between:
The shaft misalignment expected must be taken into account
when the connection between the components and the low or
high speed shaft is selected. Guidelines and limits for compen-
sation of shaft misalignment can be obtained from the manufac-
turer of the connecting element.
*B0'43B;;B33335
.
D
*B0'43B;;B33337
.
Z
Axial misalignment
Angular misalignment
*B0'43B;;B33336
.
U
Radial misalignment
© Siemens AG 2016