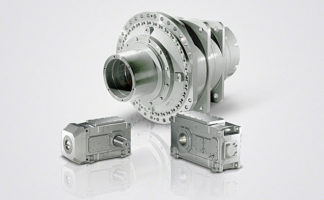
FLENDER Standard Couplings
Fluid Couplings — FLUDEX Series
13/7
Siemens MD 10.1 · 2015
General information
13
Axial retention
Axial retention is provided by a set screw or end washer with a
retaining screw for shaft ends to DIN 748/1 long with a centering
thread to DIN 332/2. Other methods must be specified in the
order, using the article number with
"-Z"
and order code
"Y99"
with plain text specification, unless ordering options are avail-
able.
Bore and keyway width tolerances are specified in catalog
section 15.
Weights specified in the dimension order tables apply to maxi-
mum bore diameters without oil filling.
■
Configuration
Selection of FLUDEX coupling
In accordance with the requirements catalog various series,
sizes and types of FLUDEX coupling are available. The FLUDEX
coupling series is characterized by various flow chamber config-
urations, fitted delay chambers or fittings in the flow chamber.
The types are determined by the design of the add-on coupling.
This results in different starting factors and characteristics which
can be used for the most varied applications. The size is speci-
fied by stating the flow outside diameter.
When selecting, the series required for the application, taking
into account the starting factor and the characteristic, must be
selected.
Selection of FLUDEX series
FLUDEX couplings which are to be used without special condi-
tions solely as an aid to starting the motor can be selected
using
the assignment tables on page 13/12
(for
n
= 1500 rpm)
or
page13/14
(for
n
= 3000 rpm).
If special requirements, based on the operating method of the
prime mover or driven machine, are made of the coupling or the
coupling is to be used in extreme environmental conditions,
please give specific details in the enquiry or order. The form
“Technical specifications for the selection of type and size” can
be used for this purpose.
Description of the FLUDEX series
FA series – drive via the hollow shaft (impeller drive)
FLUDEX FA series couplings are basic couplings (without delay
chamber) which are driven via the hollow shaft (106) with at-
tached blade wheel (105). This enables the advantages of the
compensating chamber and the working chamber to be used to
best effect. Combinations with brake drums/disks and pulleys
can also be easily achieved. When the coupling is started, part
of the oil filling in the area of greatest slip is forced into the radi-
ally inner chambers and the compensating chamber by the
strong rotational flow. This causes the effective oil filling in the
working chamber to be reduced and the desired torque limita-
tion (approx. twice
T
N
) to be achieved during starting. By means
of additional fittings the coupling torque at the start of the start-
ing operation can be limited to approx. 1.5 times of the rated
value. During run-up to speed the compensating chamber again
empties into the working chamber, and this helps to reduce slip.
153
2/3
12
101
102
103
105
106
120
153
163
101
12
2/3
103
102
105
106
163
120
FAD
FAR
Compensating chamber
Working chamber
Part 2/3 of the flexible coupling
Flexible elements
Blade wheel (outer wheel)
Cover
Fusible safety plug
Blade wheel (inner wheel)
Hollow shaft
V-belt pulley
Filler plug
Screw plug (oil drain)
G_MD10_EN_00116
© Siemens AG 2015