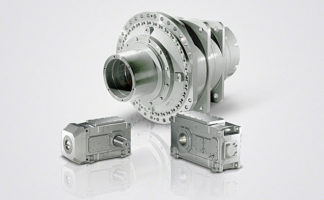
FLENDER Standard Couplings
Highly Flexible Couplings — ELPEX-S Series
11/5
Siemens MD 10.1 · 2015
General information
11
Coupling load under maximum and overload conditions
The maximum torque is the highest load acting on the coupling
in normal operation.
Maximum torques at a frequency of up to 25 times an hour are
permitted and must be lower than the maximum coupling torque.
Examples of maximum torque conditions are: Starting opera-
tions, stopping operations or usual operating conditions with
maximum load.
T
Kmax
≥
T
max
⋅
FT
Overload torques are maximum loads which occur only in com-
bination with special, infrequent operating conditions.
Examples of overload torque conditions are: Motor short circuit,
emergency stop or blocking because of component breakage.
Overload torques at a frequency of once a month are permitted
and must be lower than the maximum overload torque of the
coupling. The overload condition may last only a short while, i.e.
fractions of a second.
T
KOL
≥
T
OL
⋅
FT
Coupling load due to dynamic torque load
Applying the frequency factor FF, the dynamic torque load must
be lower than the coupling fatigue torque.
Dynamic torque load
T
KW
≥
T
W
⋅
FT
⋅
FF
⋅
Frequency of the dynamic torque load
f
err
≤
10 Hz frequency factor FF = 1.0
Frequency of the dynamic torque load
f
err
> 10 Hz frequency factor FF =
√
(
f
err
/10 Hz)
Operation in potentially explosive environments is subject to
the following restriction:
Operation with low fatigue load
The fatigue torque
T
KW
must be reduced by 70 %. In these
particular operating conditions the coupling satisfies the require-
ments of temperature class T4 D120 °C.
Operation with medium fatigue load
The fatigue torque
T
KW
must be reduced by 50 %. In these
particular operating conditions the coupling satisfies the require-
ments of temperature class T3 D160 °C.
Type EST is not permitted for application in potentially explo-
sive environments.
Checking the maximum speed
The following must apply to all load situations:
n
Kmax
≥
n
max
The maximum speed of a size depends only on the size of the
outer flange (part 3).
Checking permitted shaft misalignment and restorative
forces
For all load situations, the actual shaft misalignment must be less
than the permitted shaft misalignment.
Checking bore diameter, mounting geometry and
coupling design
The check must be made on the basis of the dimension tables.
On request, couplings with adapted geometry can be provided.
Checking shaft-hub connection
Please refer to catalog section 3 for instructions.
Checking temperature and chemically aggressive
environment
The permitted coupling temperature is specified in the Temper-
ature Factor FT table. In the case of chemically aggressive envi-
ronments, please consult the manufacturer.
0.6
FB – 1.0
© Siemens AG 2015