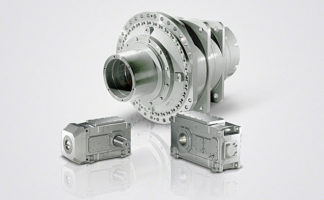
FLENDER Standard Couplings
Technical Information
2/5
Siemens MD 10.1 · 2015
2
Corrosion protection
Depending on the environmental conditions, suitable corrosion
protection must be specified for the coupling. Unless otherwise
specified in the order, steel and cast iron surfaces are shipped
with a simple preservative.
Ambient conditions
Because of the environment, the coupling has to meet a large
number of additional requirements. Couplings must be as suit-
able for use in a potentially explosive environment as for use at
a high or low ambient temperature. The environment may be de-
fined as chemically aggressive or be subject to laboratory con-
ditions or requirements of food manufacture.
ATEX and EC Machinery Directive
Wherever a potentially explosive environment cannot be ruled
out, the machinery used must meet special conditions in order
to prevent the outbreak of fire as far as possible. Within the Eu-
ropean Union, Directive 94/9/EC applies to these applications.
This directive, harmonizes the individual states' legal require-
ments for explosion prevention and clearly defines the proce-
dure for checking and circulating machines and parts. Whether
or not a machine is used in a potentially explosive atmospheres,
the manufacturer is required under EC Machinery Directive
2006/42/EC to assess and as far as possible prevent hazards
which may arise from his product.
The operator has an obligation to ascertain whether an environ-
ment is potentially explosive. Details of this are laid down in
Directive 1999/92/EC.
The manufacturer is responsible for ensuring that the product is
safe as defined in the EC Machinery Directive and conforms to
Directive 94/9/EC if the EX requirement is specified by the oper-
ator.
The drive train mostly comprises individual pieces of equipment
which are put together to form a subassembly. If the individual
pieces of equipment, such as motor, coupling, gear unit or
driven machine conform to Directive 94/9/EC, the manufacturer
of the overall unit can limit the risk assessment to the additional
hazards which arise from the combination of different individual
pieces of equipment. The hazards which can arise from the indi-
vidual pieces of equipment are assessed by the relevant suppli-
ers.
The Directive 2014/34/EU of the European Parliament and of the
Council of 26 February 2014 on the harmonisation of the laws of
the Member States relating to equipment and protective systems
intended for use in potentially explosive atmospheres will super-
sede the Directive 94/9/EC of 23 March 1994 with effect from
20 April 2016.
The following applies to the products shown in this brochure with
a suitable for intended use in potentially explosive atmospheres:
•
Products placed on the market before
20 April 2016 meet the
requirements of Directive 94/9/EC.
•
Products placed on the market from
20 April 2016 meet the re-
quirements of Directive 2014/34/EC.
The coupling series suitable for use in potentially explosive en-
vironments are marked with EX in the catalog.
FLENDER couplings are to be rated as components accord-
ing to the new EC Machinery Directive 2006/42/EC. There-
fore, Siemens do not issue a declaration of incorporation for
this products.
Overload conditions
Overload conditions are operating conditions that go beyond the
limit loads of the coupling.
Overload conditions may occur under abnormal operating con-
ditions, e.g. drive blockage, short circuit or supply deviations, as
well as under normal operating conditions, e.g. during starting
or breaking. Particularly in the case of high mass moments of
inertia of the driven machine, torques that are a multiple of the
motor starting torque may become effective during direct start-
ing or star-delta starting.
Overload conditions may damage not only the coupling but also
the entire drive train.
Overload conditions can frequently be prevent with special de-
sign measures. SIRIUS soft starters or SINAMICS frequency
converters are suitable for considerably reducing starting
torques of asynchronous motors. If drive blockages and over-
loads of the driven machine cannot be ruled out, torque limiting
SECUREX couplings can prevent damage to the drive train.
Coupling behavior under overload conditions
Coupling behavior under overload where the torque is consider-
ably above the limits of use of the coupling concerned is deter-
mined by the engineering design of the coupling series.
The ZAPEX, ARPEX, N-EUPEX, RUPEX and N-BIPEX coupling
series can withstand overloads until the breakage of metal parts.
These coupling series are designated as fail-safe. Coupling
types which can withstand overload, i.e. fail-safe types, are used
e.g. in crane systems. In case of coupling breakage due to over-
loads, the splintering metall parts may cause injury to persons
and property damages.
The N-EUPEX DS, ELPEX-B, ELPEX-S and ELPEX coupling se-
ries throw overload. The elastomer element of these couplings is
irreparably damaged without damage to metal parts when sub-
jected to excessive overload. These coupling series are desig-
nated as non-fail-safe. The types that fail can be fitted with a fail-
safe device. This component enables emergency operation,
even after the rubber element of the coupling has been irrepara-
bly damaged.
The fluid couplings of the FLUDEX series withstand a load for a
short time. Persistent overload causes the FLUDEX coupling to
heat up beyond limits, causing the fuse to operate and so emp-
tying the coupling and interrupting the torque transmission.
Torsional and bending vibrations
On drives which are prone to torsional and bending vibrations,
measurements or calculations such as natural frequency calcu-
lations, torsional vibration simulations or bending vibration cal-
culations are necessary.
The drive train may, depending on complexity, be regarded as a
two-mass vibration-generating system or N-mass vibration-gen-
erating system. The vibration-generating masses are defined by
the rotating bodies and the couplings by the coupling stiffnesses
and shaft stiffnesses. The effect of torsional vibration excitations
on the behavior of the system is calculated.
Torsional vibration excitations may occur during the starting of
an asynchronous motor, during a motor short circuit or in diesel
engine drives. Bending vibrations may be critical if the coupling
is insufficiently balanced and/or at an operating speed close to
the critical speed.
The details needed for calculating torsional vibration are speci-
fied in the coupling catalog:
•
Dynamic torsional stiffness
•
Damping (specification of the damping coefficient
ψ
or Lehr's
damping D =
ψ
/4
π
).
•
Mass moment of inertia of the coupling halves.
© Siemens AG 2015