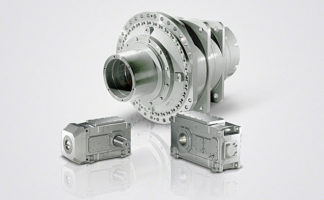
FLENDER Standard Couplings
Flexible Couplings — N-EUPEX and N-EUPEX DS Series
General information
7/8
Siemens MD 10.1 · 2015
7
Power ratings of the N-EUPEX DS series
Flexibles of sizes 66 to 272 are of the compound type with a hard core and soft thrust pieces.
Sizes 305 to 556 are completely made of 90 ShoreA NBR material.
For maximum coupling torque:
T
Kmax
= 2.0
⋅
T
KN
For coupling overload torque:
T
KOL
= 3.0
⋅
T
KN
For coupling fatigue torque:
T
KW
= 0.15
⋅
T
KN
Torsional stiffness and damping
The values stated in the above table apply to a capacity utiliza-
tion of 50 %, an excitation amplitude of 10 %
T
KN
with the fre-
quency 10 Hz and an ambient temperature of 20 °C. Dynamic
torsional stiffness is dependent on load and increases in propor-
tion to capacity utilization. The following table shows the correc-
tion factors for different rated loads.
C
Tdyn
=
C
Tdyn 50 %
⋅
FKC
The damping coefficient is
Ψ
= 1.4
Torsional stiffness and damping is further dependent on the am-
bient temperature and the frequency and amplitude of the tor-
sional vibration excitation. More precise torsional stiffness and
damping parameters on request.
With elastic couplings the manufacturing process of the rubber
elements and their aging primarily influence the rigidity value
C
Tdyn
. For this reason calculation must be made with a tolerance
for the dynamic rigidity of
±
20 %. The specified damping coeffi-
cient
Ψ
is a minimum value with the result that the damping per-
formance of the coupling corresponds at least to the specified
value.
Permitted shaft misalignment
The permitted shaft misalignment depends on the operating
speed. As the speed increases, lower shaft misalignment values
are permitted. The following table shows the correction factors
for different speeds.
The maximum speed for the respective coupling size must be
noted!
Δ
K
perm
=
Δ
K
1500
⋅
FKV
For fitting, a maximum gap dimension of S max. = S +
Δ
S and a
minimum gap dimension of
S min. = S –
Δ
S are permitted.
Shaft misalignments
Δ
K
r
and
Δ
K
w
may occur simultaneously.
Size
Rated torque
Torsional stiffness at
50 % capacity utilization
Assembly
Permitted shaft misalignment at
speed
n
= 1500 rpm
Gap dimension
1)
Radial
Angle
T
KN
C
Tdyn
Δ
S
Δ
K
r
Δ
K
w
Nm
kNm/rad
mm
mm
°
66
19
0.73
1.0
0.2
0.15
76
34
1.36
1.0
0.2
0.15
88
60
2.62
1.0
0.2
0.12
103
100
4.00
1.0
0.2
0.12
118
160
6.30
1.0
0.2
0.10
135
240
10.5
1.0
0.25
0.10
152
360
13.6
1.0
0.25
0.10
172
560
27.2
2.0
0.3
0.10
194
880
47.0
2.0
0.3
0.10
218
1340
70.0
2.0
0.3
0.09
245
2000
106
2.0
0.35
0.09
272
2800
149
2.5
0.35
0.08
305
3900
214
2.5
0.4
0.08
340
5500
350
2.5
0.4
0.08
380
7700
480
2.5
0.5
0.08
430
10300
730
2.5
0.5
0.08
472
13500
990
2.5
0.6
0.08
514
16600
1270
2.5
0.6
0.07
556
21200
1540
2.5
0.65
0.07
Capacity utilization
T
N
/
T
KN
20 %
40 %
50 %
60 %
70 %
80 %
100 %
Correction factor FKC
0.7
0.9
1
1.1
1.2
1.3
1.5
1)
Does not apply to type HDS.
Speed in rpm
500
1000
1500
3000
Correction factor FKV
1.7
1.2
1.0
0.7
© Siemens AG 2015