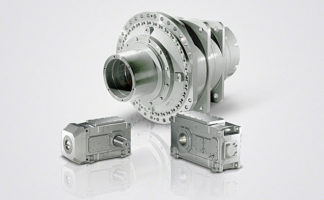
FLENDER Standard Couplings
Technical Information
2/4
Siemens MD 10.1 · 2015
2
Example:
Coupling speed = 1450 rpm
required balancing quality level G 6.3
e
perm.
= 9600
⋅
= 9600
⋅
μ
m
Thus, the required eccentricity of center of gravity is 41.7
μ
m.
The fine balancing with a maximum eccentricity of center of
gravity of 40
μ
m fulfills this requirement; therefore, the order
code W02 has to be specified when ordering.
For many applications the following balancing quality recom-
mendation applies:
Peripheral speed
v
in m/s
Coupling outer diameter
DA
in mm
Coupling speed
n
in rpm
Coupling length
LG
in mm
The following standards on balancing must be observed:
•
couplings are balanced in subassemblies.
•
hub parts without finished bore are unbalanced.
•
the number of balancing levels (one- or two-level balancing) is
specified by Siemens.
•
without special specification balancing is done in accordance
with the half-parallel-key standard. Balancing in accordance
with the full-parallel-key standard must be specified in the
order number.
•
for FLUDEX couplings special balancing standards specified
in Section 13 apply.
•
ARPEX couplings in standard balancing quality are unbal-
anced. Thanks to steel components machined all over and
precisely guided adapters the balancing quality of standard
balancing is nearly always adhered to.
Shaft-hub connections
The bore and the shaft-hub connection of the coupling are de-
termined by the design of the machine shaft. In the case of IEC
standard motors, the shaft diameters and parallel key connec-
tions are specified in accordance with DIN EN 50347. For diesel
motors, the flywheel connections are frequently specified in ac-
cordance with SAE J620d or DIN 6288. Besides the very widely
used connection of shaft and hub with parallel keys to DIN 6885
and cylindrically bored hubs, couplings with Taper clamping
bushes, clamping sets, shrink-fit connections and splines to
DIN 5480 are common.
The form stability of the shaft/hub connection can only be dem-
onstrated when shaft dimensions and details of the connection
are available. The coupling torques specified in the tables of
power ratings of the coupling series do not apply to the shaft-
hub connection unrestrictedly.
In the case of the shaft-hub connection with parallel key, the cou-
pling hub must be axially secured, e.g. with a set screw or end
washer. The parallel key must be secured against axial displace-
ment in the machine shaft.
All Siemens couplings with a finished bore and parallel keyway
are designed with a set screw. Exceptions are some couplings
of the FLUDEX series, in which end washers are used. During
assembly, Taper clamping bushes are frictionally connected to
the machine shaft.
Assembly
Assembly, start-up, maintenance and servicing of the coupling
are described in the operating instructions.
Contact protection
Couplings are rotating components which can pose a risk to the
environment. Siemens prescribes fitting couplings with a suit-
able contact guard, also called a coupling guard in the operat-
ing instructions. The contact guard, must provide a firm cover to
protect against contact with the rotating coupling. The coupling
must also be protected against blows from objects striking it.
The coupling guard must enable the coupling to be adequately
ventilated. The following guidelines give information on design-
ing the contact guard: 2006/42/EC EC Machinery Directive;
EN 13463-1 Section 13.3.2.1; EN 13463-1 Section 7.4;
EN 13463-1 Section 8.1.
Maintenance
All-steel membrane couplings of the ARPEX series require no
maintenance. If the operating and mounting conditions have
been adhered to, only regular visual inspection is required.
Elastomer elements, elastomer seals and lubricants are subject
to wear through ageing and loads. To avoid damage to the cou-
pling or failure of the drive, the ZAPEX, N-EUPEX, N-EUPEX DS,
RUPEX, N-BIPEX, ELPEX, ELPEX-S, ELPEX-B and FLUDEX se-
ries must be maintained in accordance with the operating in-
structions.
On gear couplings, the lubricant must be changed at regular
intervals.
On flexible or highly flexible couplings, the torsional backlash or
the torsion angle must be checked at regular intervals under
load. If a limit value is exceeded, the elastomer element must be
replaced. It is very important to maintain couplings which are
operated in a potentially explosive environment, as couplings
which are not maintained can become ignition sources.
Standard balancing
Fine balancing
Coupling
v
= DA
⋅
n/19100
Short version with
LG
≤
3 x DA
v
≤
30 m/s
v
> 30 m/s
Long version with
LG > 3 x DA
v
≤
15 m/s
v
> 15 m/s
G 1
G 4
G 10
G 16
G 25
G 40
10
2
10
1
2
4
6
8
2
4
6
8
2
4
6
8
10
3
10
2
4
2
6
8
2
4
6
8
10
3
10
4
G 1.6
G 2.5
G 6.3
G_MD10_EN_00007a
Eccentricity of center of gravity e
perm.
in μm
Coupling speed in rpm
On request
Micro-balancing
Fine balancing
Standard balancing
G
n
---
6.3
1450
© Siemens AG 2015