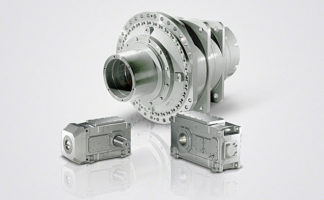
FLENDER Standard Couplings
Technical Information
2/3
Siemens MD 10.1 · 2015
2
Balancing
Because of primary shaping processes and machining, the cou-
pling components are manufactured with a mass distribution
about the axis of rotation of the motor, gear unit or driven ma-
chine which is not always ideal.
Balancing means improving the mass distribution of a rotating
body so that it rotates on its bearings with a sufficiently limited
effect of free centrifugal forces.
The imbalance force increases linearly with the distance be-
tween the center of gravity of the body and the axis of rotation,
the weight of the body and the rotor speed squared.
F = imbalance force
S = center of gravity of the body
e = distance of center of gravity of body from the pivot axis
In the case of rotating unbalanced coupling parts rotary, imbal-
ance forces develop which impose loads on the bearings of the
machine shafts and excite vibration. High vibration values on
drives are frequently detected as early as initial start-up if the
balance of the machine shafts or the mounted coupling parts is
insufficient or the balancing specifications are incompatible. The
balance condition of the coupling can be measured on balanc-
ing machines. By adding or drilling away material, a balance
condition which meets the requirements can be achieved.
Balance quality levels
The so-called quality level G to DIN ISO 1940 indicates a range
of permitted residual imbalance from zero up to an upper limit.
Applications can be grouped on the basis of similarity analysis.
For many applications a coupling balance quality of G 16 is suf-
ficient. On drives susceptible to vibration the balance quality
should be G 6.3. Only in special cases is a better balance qual-
ity required.
Single- and two-level balancing
For discoid bodies (such as brake disks, coupling hubs) so-
called single-level balancing is carried out. The mass compen-
sation for the imbalance is undertaken at a single level only. For
historical reasons single-level balancing is also known as static
balancing. On long bodies such as adapters mass compensa-
tion must be implemented at two levels to reduce the couple im-
balance. Two-level balancing is carried out while the rotor body
is rotating. Historically, this is known as dynamic balancing.
Balancing standard in accordance with DIN ISO 21940-32
Besides the required balance quality, it is necessary to set stan-
dards which define how the mass of the parallel key is to be
taken into consideration when balancing. In the past, motor ro-
tors have frequently been balanced in accordance with the full
parallel key standard. The "appropriate" balance condition of the
coupling hub was described as "balancing with open keyway" or
"balancing after keyseating". Today it is usual for the motor rotor,
as well as the gear unit and driven machine shaft, to be bal-
anced in accordance with the half parallel key standard.
Full parallel key standard
The parallel key is inserted in the shaft keyway, then balancing
is carried out. The coupling hub must be balanced without par-
allel key after keyseating. Marking of shaft and hub with "F" (for
"full").
Half parallel key standard
The balancing standard normally applied today. Before balanc-
ing, a half parallel key is inserted in the shaft and another in the
coupling hub. Alternatively, balancing can be carried out before
cutting the keyway. The balanced parts must be marked with an
"H". This marking can be dispensed with if it is absolutely clear
which parallel key standard has been applied.
No parallel key standard
Balancing of shaft and coupling hub after keyseating, but with-
out parallel key. Not used in practice. Marking of shaft and hub
with "N" (for "no").
The length of the parallel key is determined by the shaft keyway.
Coupling hubs may be designed considerably shorter than the
shaft. To prevent imbalance forces caused by projecting parallel
key factors when balancing in accordance with the half parallel
key standard in the case of applications with high balancing
quality requirements, grooved spacer rings can be fitted or
stepped parallel keys used.
Siemens Balancing Standard
The balancing quality level, together with the operating speed,
results in the maximum permissible eccentricity of the center of
gravity of the coupling or the coupling subassembly. In the
Siemens article number the balancing quality can be preset with
the help of the order code. Additionally, also the balance quality
level to DIN ISO 1940 can be preset together with the operating
speed belonging to it, which then be taken as priority.
The procedure to determine the Siemens balancing quality
is as follows:
Operating speed and required balancing quality level are known
from the application. Using these values, the required eccentric-
ity of the center of gravity can be calculated using the specified
formula context or the following graph. The eccentricity of the
center of gravity of the coupling must be less than the required
eccentricity of the center of gravity to achieve the required bal-
ancing quality. The associated article number must be stated in
the order; only if standard balancing has been selected is the ar-
ticle number to be dispensed with
e
coupl
≤
e
perm.
permitted:
Eccentricity of center of gravity
e
perm.
in
μ
m
Eccentricity of center of gravity
of the coupling
e
coupl
in
μ
m
Balancing quality level
G
in mm/s
Coupling speed
n
in rpm
Order code to determine the balance quality level to
DIN ISO 1940 and the operating speed:
Y95 {G = __; n = __rpm}.
<
*B0'43B;;B33339
)
U
D
=
:
H
Eccentricity of center of
gravity of coupling
e
coupl
Siemens
balancing quality
Order code
maximum 100
μ
m
standard balancing
without specification
maximum 40
μ
m
fine balancing
W02
maximum 16
μ
m
micro-balancing
W03
better than 16
μ
m
special balancing
on request
e
perm
9600
G
n
---
⋅
=
© Siemens AG 2015