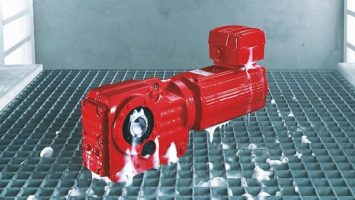
< Previous Sew Eurodrive products | Products index | Next Sew Eurodrive products >
Explosion-proof industrial gear units
Explosion protection according to ATEX
04
ATEX designs of industrial gear units: (Group II, categories 2/3G and 2/3D, zones 1, 21, 2 and 22) | – X series – X series – bucket elevator drives – MC series – P series – P-X series – M1N series |
Gear units comply with Directive 2014/34/EU (ATEX), equipment group II, categories 2G, 2D, 3G or 3D for use in zones 1, 2, 21 or 22. The X series is also available for equipment group I, category M2. | – For use on the European market – Accepted in China – Accepted in Russia in conjunction with EAC certificates (successor to GOST-R) |
Protection types | – Protection type “c”: Protected by safe construction (design safety), EN13463-1 and -5 – Protection type “k”: Protected by liquid immersion, EN13463-1 and -8 |
4.5 Segmented girth gears
NEW: Segmented girth gears
Segmented girth gears
Features | – Girth gear pitch diameter up to about 16 m* – Maximum width 600 mm – Maximum power 4000 kW per pinion – Maximum pitch line velocity 6 m/s – Girth gear module 20, 25, 30, and 40 mm – Calculated according to ISO standard 6336 (AGMA on request) |
Advantages | Highly segmented girth gears, segments 1. Easy casting The design of the feeders and the use of heat sinks guarantee a seamless casting quality even with critical segments 2. Convenient handling - The handling of the individual segments and component groups is simplified both in the factory and at the construction site - No need for special transportation arrangements: segmented girth gears can be transported in standard containers 3. Optimized quality assurance - The minimized size brings also cost advantages when it comes to the scrapping of blanks - Flawless blanks can be used without additional welding or oversizing 4. Precise pitch accuracy - The segmented girth gears from SEW-EURODRIVE guarantee the initial pitch accuracy of ISO 8 (AGMA 9) - Because of the high pitch accuracy, the vibrations of the girth gears are kept to a minimum 5. Easy replacement If a segment is damaged, it can be exchanged without dismantling the whole ring 6. Reduced weight - ADI** has an over-average contact fatigue strength due to its cold work hardening Features - These features combined with an appropriate girth gear size enable a compact and lighter design compared to the traditional solution - The low weight is important for the handling and the assembly of the girth gear as well as the achievable circumferential velocity 7. Increased service life With the correct dimensioning, load and lubrication, an ADI** girth gear is nearly wear-free 8. Shorter delivery time The small segments allow for fast production and short delivery times |
* Larger diameters are possible. Contact SEW-EURODRIVE.
** Made of tempered ductile iron