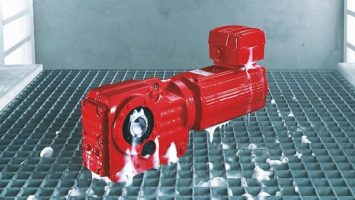
< Previous Sew Eurodrive products | Products index | Next Sew Eurodrive products >
07
Parameterizable MOVIVISION plant software
Features – Intuitive software solution for system manufacturers and operators
– Simple and fast startup of a drive system
– Can be used at any time and any place
– No special programming knowledge is required – only parameters have to be entered
Ú More information regarding software: Pages 326 – 329
INDUSTRIAL
08 COMMUNICATION
8.1 Industrial ETHERNET 298
8.2 Conventional fieldbuses 301
8.3 SEW-EURODRIVE system buses 303
8.4 Communication modules
and fieldbus tools 305
8.5 Safe communication 306
08
8.1 Industrial Ethernet
Industrial ETHERNET
One cable – numerous possibilities | – High transmission rate – Widespread medium – Enables the use of IT technology, such as e-mail for notification if an error occurs, and diagnos- tics for the implemented components using the Internet Explorer – Ensures vertical data communication with the control level with high bandwidth as well as hori- zontal process data communication between controller and application (e.g. drive inverters) – Comprehensive service from SEW-EURODRIVE for process data communication |
Advantages | – Vertical and horizontal communication using Industrial ETHERNET – Real-time capable process data communication between controller and drive technology components (soft real time) with 10 process data words (each direction) – Fast data transfer with 100 Mbit/s – Diagnostics of drive technology via Internet Explorer, for example – Programming and diagnostics for the drive technology can be carried out via Ethernet, which makes remote maintenance easy to handle – Broadband data communication between the control level and field level – Control and engineering combined in one bus system, saving costs for installation and maintenance – Fast system integration |
Functions | – Process data communication by means of protocol, either PROFINET IO/RT, EtherNet/IP™, Modbus TCP or EtherCAT, for simple and fast data exchange between the control and field levels – Control and diagnostics via Ethernet – local operation, diagnostics, and maintenance at the field level – Integrated web server (not EtherCAT) to diagnose the drive technology via Internet Explorer – Central data backup at control level – Parameterization and programming using MOVITOOLS MotionStudio via Ethernet – Reduction of installation costs and maintenance due to installation of only one diagnostic bus or engineering bus system |
299
Overview of fieldbus options
Industrial ETHERNET PROFINET EtherNet/IPTM Modbus TCP EtherCAT
Inverter technology: Control cabinet installation and wall mounting
MOVITRAC LTE
basic inverter
DFE32B/UOH option DFE33B/UOH option DFE33B/UOH option DFE24B/UOH option
MOVITRAC LTP
standard inverter
Options
– DFE32B/UOH
– Controller DHR
– LTFE32A
Options
– DFE33B/UOH
– Controller DHR
– LTFE33A
Options
– DFE33B/UOH
– Controller DHR
– LTFE31A
Options
– DFE24B/UOH
– LTFE24A
Inverter technology: Control cabinet installation
MOVITRAC B
standard inverter
Options
– DFE32B
– DFE32B/UOH
– DFS21B/PROFIsafe
Options
– DFE33B
– DFE33B/UOH
Options
– DFE33B
– DFE33B/UOH
Options
– FSE24B
– DFE24B
– DFE24B/UOH
MOVIDRIVE B
application inverter
Options
– DFE32B
– DFS21B/PROFIsafe
DFE33B option DFE33B option DFE24B option
MOVIAXIS
multi-axis servo inverter
Options
– UFR41B
– Controller DHR
Options
– UFR41B
– Controller DHR
Options
– UFR41B
– Controller DHR
XFE24A option